Our responsibility in figures.
Based on the GRI standards, we provide information and facts about the economic, ecological and social effects of our work. GRI stands for Global Reporting Initiative. This international, non-profit organisation is dedicated to the development and dissemination of a global framework for sustainability reporting. We have had our information verified by an independent expert (GRI 102-56) and have marked each of our assessments with symbols:
GRI disclosure fully reported, data verified: | ||||
GRI disclosure fully reported, data not verified: | ||||
GRI disclosure partly reported, data verified: | ||||
GRI disclosure partly reported, data not verified: |
The explanations are displayed in the GRI index as soon as you move your mouse pointer over the symbols.
GENERAL DISCLOSURES
We, Pöppelmann Holding GmbH & Co. KG, are a family-run company with headquarters in Lohne (Lower Saxony), Germany. Unless otherwise stated, the information reported relates to Pöppelmann Holding GmbH & Co. KG and its subsidiaries Pöppelmann GmbH & Co. KG Kunststoffwerk – Werkzeugbau and Pöppelmann Kunststoff-Technik GmbH & Co. KG in Lohne.
Since 1949, Pöppelmann has developed into one of the leading manufacturers in the German plastics processing industry with six production sites and approx. 650 injection moulding machines, thermoforming plants and extruders. The quality “made by Pöppelmann” is coveted in over 90 countries thanks to more than 2,500 highly qualified employees around the globe – our "Pöppelmen and Pöppelwomen".
Our company is organised into four business divisions.
Pöppelmann KAPSTO® has developed and produced plastic protective elements since 1957, offering around 5,000 different versions. Some 3,000 of these are standard articles while approx. 2,000 are custom orders.
Pöppelmann K-TECH® has developed and produced injection-moulded technical parts with the highest quality standards for the automotive and electrical industries as well as for machine and equipment manufacturers since 1962. It currently has around 2,600 active products.
Pöppelmann TEKU® has produced and developed plant and cultivation systems for commercial horticulture since 1970. The company supplies approx. 2,400 variants of some 750 standard products.
Pöppelmann FAMAC® has developed and produced technical functional parts and packaging for the food, pharmaceutical and cosmetics industry since 1998, as well as for medical engineering in approx. 1,700 designs.
We have also had our own mould making facility since 1957. It guarantees high quality and flexibility in mould production and repair.
The company’s headquarters have always been at home in Lohne, Lower Saxony.
We have four plants at our main location in Germany – three in Lohne and one in Holdorf. We also have one production plant in France and another in the USA. Sales offices in Spain, Poland, Denmark, Czech Republic, Italy, Romania and China sell our products. The information in the report refers to our sites in Germany (see GRI 102-45).
Our company, Pöppelmann Holding GmbH und Co. KG, is 100 % family-owned. It also owns 100 % of both subsidiaries: Pöppelmann GmbH & Co. KG Kunststoffwerk – Werkzeugbau and Pöppelmann Kunststoff-Technik GmbH & Co. KG. The same management team governs both the holding and the two subsidiaries. The ultimate controling body is the advisory board.
Our customers come from over 90 counties and are active in a wide range of sectors and industries. As a plastics-processing company, we supply products to countless markets all over the world, although mainly in the automotive, food, pharmacy, medical, machine construction and commercial horticulture sectors.
Markets served
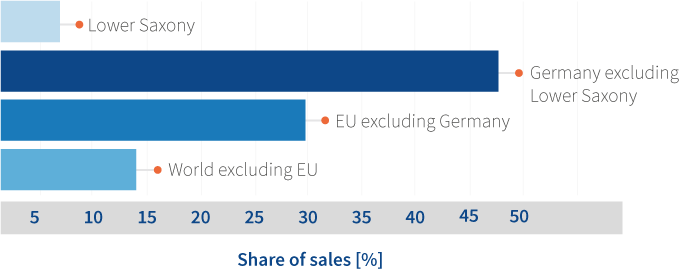
We employ more than 2,500 staff at our six production sites worldwide. A total of 2,275 employees work at our four plants in Germany, where around 5,600 products are manufactured. We use approximately 650 plastics-processing machines in our four divisions.
Financial details like sales or profit and loss figures are subject to confidentiality in accordance with our internal regulations and are not published.
During recent years, company growth has caused our total number of employees to increase significantly. As of December 2018, we have a total of 2,275 employees at our sites in Lohne and Holdorf. We also employ seasonal, temporary workers, especially students. This predominantly occurs during academic holidays.
Employee structure
2017 |
2018 |
|
---|---|---|
Employees (total)* | 2,065 | 2,275 |
of which male | 1,651 | 1,801 |
of which female | 414 | 474 |
permanent | 1,770 | 1,842 |
of which male | 1,452 | 1,498 |
of which female | 318 | 344 |
temporary | 295 | 433 |
of which male | 199 | 303 |
of which female | 96 | 130 |
full-time | 1,904 | 2,095 |
of which male | 1,635 | 1,777 |
of which female | 269 | 318 |
part-time | 161 | 180 |
of which male | 16 | 24 |
of which female | 145 | 156 |
Agency workers | 0 | 0 |
Employee structure
2017 | 2018 | |
---|---|---|
Employees (total)* | 2,065 | 2,275 |
of which male | 1,651 | 1,801 |
of which female | 414 | 474 |
under 30 years of age | 690 | 779 |
of which male | 560 | 612 |
of which female | 130 | 167 |
30 to 49 years | 953 | 1,063 |
of which male | 778 | 874 |
of which female | 175 | 189 |
50 years and older | 422 | 433 |
of which male | 313 | 315 |
of which female | 109 | 118 |
In accordance with the PPx principles, our primary goal is to achieve 100 % delivery reliability and quality for all internal and external customers. We define delivery reliability as quantity and schedule reliability. The goods and services to be provided must also be made available in the right quantity and quality at the right time. Our delivery reliability is currently 94 %. We aim to increase this to 96 % by 2019. We measure quality using the rate of complaints. In 2018, it was 2.5 %. By the end of 2019, we aim to have reduced it to 1.6 %.
As part of the procurement strategy, we have set ourselves financial and non-financial goals. As a purchasing department, we are firmly committed to our social responsibility in the world (e.g. PÖPPELMANN blue®). By the end of 2025, we want to cover at least 25 % of material requirements with recycled material from closed cycles (PÖPPELMANN blue®) and a total of 60 % with recycled materials. For this purpose, each of the four divisions has developed its own goals, which they have passed on to us.
The supply chains for the four divisions differ in light of their business activities, which is why we have strategic buyers for each area in our central department. The operational procurement processes are handled in the divisions. The total number of suppliers is in the low four-digit range.
In the areas of TEKU® and KAPSTO®, we have more options to design our supply chains since we sell our products on demand-oriented and heterogeneous markets. In the K-TECH® and FAMAC® divisions, we work together with our customers, for example from the automotive and medical sectors, to find specific solutions. In these cases, the choice of possible suppliers is limited.
As a result, we have greater influence on material flows for TEKU® and KAPSTO®. Some of our products have been certified (for example with the “Blauer Engel” or Blue Angel) and we also require such certificates from our suppliers in order to ensure a completely sustainable supply chain. In relation to this, we have made great progress in both divisions. For the TEKU® Circular Blue plant pots, we have succeeded in completely closing the material cycle through the use of post-consumer recycled material from the dual system (household kerbside recycling). For KAPSTO®, we are currently creating B2B cycles to recover closure elements from our customers to process and reuse as material for new closure elements.
Overall, raw materials (35 %), investments and tools (30 %) and purchased parts (10 %) make up three quarters of the goods purchased. In the area of TEKU®, we procure recycled materials from the raw material market and supply a large number of product series with just a few material types. In the other divisions, we use a significantly larger number of different material types. Some of our customers prescribe specific materials and thus the supply chain. Added to this are customers’ purchased part and packaging regulations, which make the supply chain more complex.
We define specific goals for our suppliers and check them ourselves through audits and visits. These not only include traditional aspects such as delivery reliability, quality and costs, but also other considerations such as sustainability. We are currently working together with our suppliers to eliminate unnecessary packaging in advance. We also ask them to consider the recyclability of the material when choosing their input flows.
Supply chain, purchase volumes
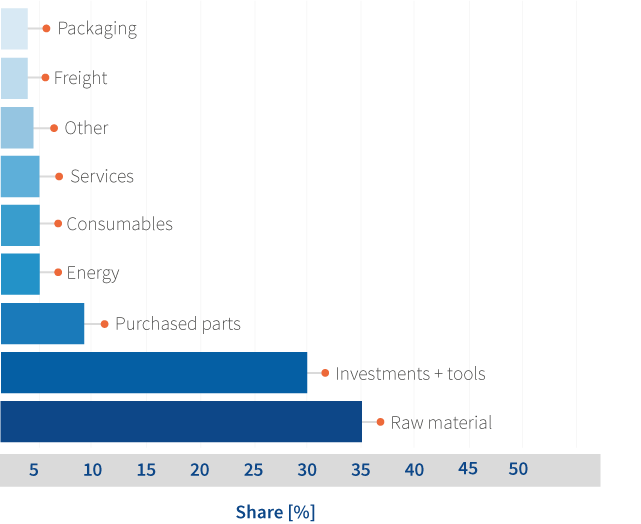
In the last few years, plants 2 and 3 have been extended. In 2017, the FAMAC food packaging production area moved from plant 1 to the new production hall 33 in plant 3, which was completed in 2016. In 2018, the new production hall 41 in plant 2 was also completed. The ownership structure did not change during this reporting period.
Sustainability-related aspects (such as resource efficiency and origin) are also becoming increasingly important for us. As a result, we now use raw material sources that we did not even consider a few years ago, such as the dual system (household kerbside recycling). We are currently focusing on the TEKU® division, although this will be expanded to the other areas in the future.
In accordance with our environmental guidelines, we are committed to assuming responsibility for the entire product life cycle – from manufacturing to recycling. The best possible ecological compatibility should be achieved whilst simultaneously considering economic aspects. In the development of our products, we take relevant environmental issues into account and influence the life cycle while considering energy consumption, raw material consumption and disposal.
Our precautionary approach primarily concerns the avoidance of incidents that harm the environment or the health of employees. Instructions for conduct in emergencies are specified in the fire protection regulations, hazard prevention plan and the accident and alarm plans. Within the framework of the new risk management, risks are systematically recorded, assessed and the necessary measures implemented. Risk management includes, for example, extreme natural events (e.g. flooding) or damage to the neighbourhood and environment (e.g. as a result of a major fire).
We participate in the following initiatives:
No. | Name | Role of PP | Description (purpose) |
---|---|---|---|
1 | Benefits of Nature | Simple member | Initiative for the promotion of a sustainable horticultural industry |
2 | Institute for Plastics Processing in Industry and Craft at RWTH Aachen University (IKV) | Simple member | Promotion of the work of IKV Aachen |
3 | FSKZ e. V., funding body for SKZ Kunststoff-Zentrum | Norbert Nobbe is a member of the board of directors | Promotion of the work of SKZ |
4 | Gesellschaft der Freunde und Förderer des OFFIS e.V. | Simple member | Promotion of innovation in information and communication technology |
5 |
Freunde und Förderer der PHWT e. V. Prof Carsten Bye |
Simple member | Promotion of the work of the PHWT Centre for Materials and Technology |
6 | PHWT Mitglieder- und Unternehmensverbund e.V. | Simple member | Promotion of training at PHWT |
7 |
Forschungsverbund ZWT e. V. |
Simple member | Promotion of collaboration between regional companies and PHWT and amongst each other |
8 | Verbund Oldenburger Münsterland e. V. | Simple member | Strengthening the Cloppenburg and Vechta districts as an economic region and travel destination |
9 | RAL Gütegemeinschaft Rezyklate aus haushaltsnahen Wertstoffsammlungen e. V. | Member of the quality and audit committee | Promotion of the use of recycled materials in plastic packaging |
10 | DIN Deutsches Institut für Normung e. V. | Simple member | Platform for standardisation |
11 | New Plastics Economy Global Commitment | Signatory | Promotion of the circular economy |
We are a member of the following associations and advocacy groups:
No. | Name | Role von PP | Description (purpose) |
---|---|---|---|
1 | Deutsches Verpackungsinstitut e. V. (dvi) | Simple member | Network of companies in the packaging industry |
2 | WBA Aachener Werkzeugbau Akademie GmbH | Simple member | Network of toolmakers |
3 | Oldenburgische Industrie- und Handelskammer | Simple member | |
4 | Bundesverband Materialwirtschaft, Einkauf und Logistik e. V. (BME) | Simple member | Trade association for purchasers, supply chain managers and logistics |
5 |
IK Industrievereinigung Kunststoffverpackungen e. V. |
Member of the steering committee for the environment and sustainability | Network of companies in the plastic packaging industry |
6 | Industrieverband Garten (IVG) e. V. | Simple member | Horticultural industry association |
7 | GKV/TecPart - Verband technische Kunststoff- Produkte e. V. | Simple member | Network of technical plastic product manufacturers |
We assume responsibility – with competence and experience
Plastic is the material that has enabled humanity to make ground-breaking progress for more than 100 years: in medicine and in the household, in communications and in mobility. A world without plastic is unimaginable – and undesirable. Without plastic, today’s expectations in terms of living standards and conditions, hygiene and modern technology could not be maintained. Put simply, our plant pots help to keep the world green. Our food packaging makes sure that quark, spreads and salads arrive fresh at the table with reliable product quality. Our laboratory receptacles ensure flawless blood sampling. Our technical automotive components enable advances to be made in CO2-reducing lightweight construction solutions. Our protective elements protect highly complex and sensitive components against damage.
Our goal is to reconcile the market demands of our industry with our responsibility for future generations. This sustainability report illustrates how we do this as a leading company in plastics processing. In it, we outline how this aspiration impacts on our everyday work within the company as well as in the action areas of product, employees, resources and region.
We are proud of our expertise and experience in plastic. We do not have to hide what we do today to find intelligent product concepts for the world of tomorrow. At the same time, we see great potential for improvement in the future, especially in terms of a circular economy. Sustainable production can only succeed if material cycles are closed, and it is this conviction that drives us forward.
With our PÖPPELMANN blue® initiative, we took our first steps in this direction very early on and are already reaping initial success. But there is a long road ahead. We cannot overcome it alone; it demands the collaboration of all parties involved in politics, science, business and society. Even against this background, we are pleased about the current controversial discussion surrounding our material, plastic. It shows that there is great interest in our work and can provide crucial motivation for the development of sustainable product solutions.
Those who speak of sustainability are referring to an ecological balance, economic security and social fairness. We are determined to make our contribution in realising this comprehensive concept for the future. Working on the sustainability strategy and report helps us to set the right course in good time.
We would like to thank everyone inside and outside our company who has supported us on this journey of self-assurance and route planning for the future through discussions and pointers, criticism and suggestions.
We have given our report the title “We do it. Better. In joint responsibility for tomorrow.” This is the benchmark by which we measure our performance.
Executive board
Norbert Nobbe, Matthias Lesch, Henk Gövert
For our business model, sustainability means closing cycles. We see the “circular economy” business model as a long-term, strategic priority that is conducive to and necessary for our future viability. In the TEKU® division, Pöppelmann blue® is the starting point of this strategy. Extending the initiative to all areas of the company gives us a clear opportunity to strengthen our pioneering role. We also want to demonstrate that plastic can be a sustainable material.
In a global market shaped by price pressure, this gives Pöppelmann the opportunity to stand out with the quality and sustainability of our products and brands. The prerequisites for this are investments in sustainability innovations. These range from process optimisations to larger business model innovations.
Our “circular economy” business model focuses on the use of recycled materials. This is why we will do even more to promote recycled materials across the market, including through networks and projects with all stakeholders from all sectors. Acceptance amongst the population will play a key role in this, since plastic is currently viewed extremely critically in public discussions. This not least also has an influence on political decisions.
It is therefore all the more important to maintain transparent and active stakeholder dialogue – which will be decisive for the entire industry. The initiation and promotion of cooperation and networks is only one part of transparent and active communication.
In addition to sustainability, digitalisation is a trend that is already making its mark on today’s society. Digitalisation brings challenges and opportunities, not only for processes and products, but also in terms of collaboration. For a company with strong regional roots like Pöppelmann, the challenge is to preserve jobs while simultaneously encouraging digitalisation and offering staff new perspectives. Only by acting as a fair and attractive employer can Pöppelmann remain fit for the future.
Our entire corporate policy has been adapted to the Pöppelmann guidelines (PPx), which were newly defined in 2017. PPx describes the comprehensive management system and the strategic direction of our organisation.
We do it. Better. This is our standard for all that we do. This standard and our four principles are the most important components of our corporate policy and our PPx management system. They provide us with a joint understanding of Pöppelmann’s internal and external direction as a foundation and framework for our actions, and ensure that we live up to our responsibility as one of our industry’s leading companies.
The four principles are:
1. We create added value for our customers.
2. We are successful because of our employees.
3. We actively design our future with creativity and innovation.
4. We achieve excellent results in the long term.
The goals of the divisions and the central departments are based on these four principles and are illustrated in the form of a PPx traffic light . In the PPx traffic light, each principle is accompanied by the aim, markets, the Pöppelmann difference, the necessary initiative and measures and the results to be achieved.
Our code of conduct describes the responsible handling of the topics of global guidelines, ethical and social principles, sustainable environmental and climate protection as well as antitrust and competition law requirements. The code applies to all employees, including the executive board and managers of all companies in the Group. Disciplinary action will be taken for any violations uniformly and consistently. In addition to all staff members, customers, suppliers and other service providers can report violations anonymously. They can do this in writing to the compliance officer or via e-mail to a specially created e-mail address.
The code of conduct will soon be published on our website.
Since 01.09.2019, the Executive Board of Pöppelmann Holding GmbH & Co. KG has consisted of three managing directors with equal rights, Norbert Nobbe (Technology, Supply Chain and Quality), Matthias Lesch (Marketing, Sales, Innovation and Procurement) and Henk Gövert (Finance, HR and IT). (see also GRI 102-20)
In light of its legal form, there is no supervisory board at Pöppelmann Holding GmbH & Co. KG. The control and advisory board of the executive board is our company advisory board, which consists of five members:
• Catherine Vitale (Chairperson; business/tax consultant and shareholder)
• Dr. Karl-Heinz Bourdon (Deputy Chairperson; Senior Vice President Integration at KraussMaffei Technologies GmbH)
• Maximilian Forst (shareholder)
• Hans Höffmann (entrepreneur from Vechta)
• Dr. Frank Hannes (lawyer and tax advisor)
The advisory board meets four times a year and is responsible for monitoring the executive board and ensuring the interests of shareholders. It is also responsible for the company’s strategic orientation and investments.
The executive board is jointly responsible for economic, ecological and social issues.
The executive board engages in dialogue with stakeholders through a variety of methods. For example, the TOP Industry Forum held on our premises in October 2018 was dedicated to the topic of sustainability. The event enabled us to exchange ideas and experiences with customers, competitors and suppliers. The executive board also engaged in dialogue with local residents at Pöppelmann Researchers’ Sunday in the Lohne Industrial Museum in November 2018. It is hoped that this format will be repeated at least every two years. Feedback from the dialogue will be passed on to the advisory board.
Together with the advisory board and shareholders, the executive board defines values, principles, strategy and goals.
The risk management procedures for economic, ecological and social issues are monitored by the advisory board. The advisory board receives regular reports and advises the executive board.
The sustainability report was approved by the executive board.
Our most important stakeholders include internal stakeholders such as employees, the advisory board and shareholders as well as the executive board and external stakeholders such as customers, suppliers, competitors and applicants/specialists and public politics. We also included these in our stakeholder dialogue. The most important stakeholder groups are shown in the following illustration.
List of stakeholder groups
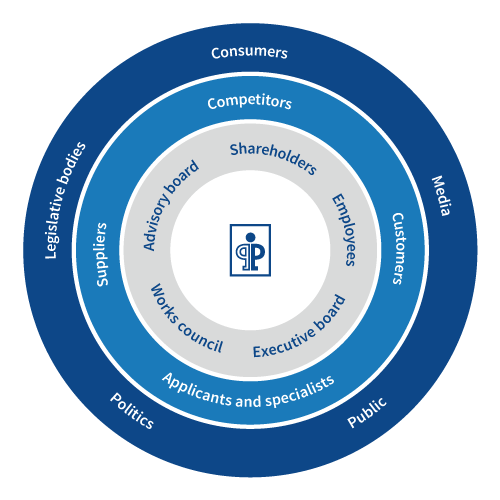
All employees are exempt from collective wage agreements. We will continue to adhere to our employment policy in this respect in the future. This disclosure is therefore not applicable for us.
We have identified our most important stakeholders using recognised methods. For this purpose, interest in and influence on sustainable business at Pöppelmann was assessed for various stakeholders and presented as a matrix. Stakeholders who have the greatest interest in and influence on our activity from an economic, ecological and social point of view were considered as particularly important.
There is constant exchange between the executive board and the works council in representation of employees. A meeting is convened twice a year where the executive board can be informed of important issues and employees can ask questions. These meetings are supplemented at irregular intervals by the ‘blue sofa’ format, which provides all employees with the opportunity to sit down on the sofa and chat to representatives from the executive board. Important information is posted on the bulletin boards and the Intranet. We engage in daily exchange with customers and suppliers via telephone, e-mail or in person. As part of customer dialogue, we have been carrying out anonymous customer surveys every two years since 2017.
In October 2018, we held the TOP Industry Forum on our premises. This event enabled us to intensify our dialogue with customers, suppliers, market participants and local politicians.
We also organised the first Researchers’ Sunday in Lohne Industrial Museum in November 2018. Dialogue with local residents was a key component of the event. The next Researchers’ Sunday is due to take place in November 2020.
We held interviews with customers, suppliers, competitors and local politicians for the development of our sustainability strategy.
You can find out more about our expert dialogue on sustainability in stakeholder dialogue.
For our employees, secure, good jobs with long-term perspectives are of utmost importance. Important aspects in this respect are training and further education, alongside a transparent information policy. Our customers value innovative, high-quality and sustainable products. The focus here is on the use of recycled materials and recyclability, as well as climate- and energy-efficient production and transparent supply chains. For local residents and politicians, willingness to enter into dialogue on issues such as noise, odours, traffic and water and land use is a major concern. Open and fair communication at eye level is extremely important to our suppliers. Issues raised by stakeholders were taken into account in the materiality analysis. For the further development of the sustainability strategy and the next sustainability report, we want to further systematise and expand our stakeholder dialogue.
In this sustainability report, we focus on our production and administrative locations in Germany, since we have all the necessary data from these locations. In the future, we also plan to include our overseas locations, especially our production sites in the USA and France.
The key topics of our business activity were defined in several steps. After an initial environment and risk analysis, we identified a selection of company- and sector-specific issues that are relevant to us. We supplemented these with the information contained in the GRI standard. With consideration given to our most important stakeholders, we have created an initial list of topics.
In a series of workshops, the sustainability steering team, which is made up of representatives from the relevant companies areas, discussed and summarised these issues. We then conducted stakeholder dialogue with external experts, including customers, market participants, local politicians and media representatives.
The results of this dialogue served to sharpen our materiality analysis further. The result: four fields of action with 12 topics that make up our sustainability strategy and about which we will report in the future.
As the result of the analysis shown in Disclosure 102-46, we identified 12 key topics that have been assigned to four areas of action: product, employees, resources and region. These represent the pillars of our sustainability strategy, which will guide our thoughts and actions in everyday life in the coming years. At the time of writing this report, we are formulating general and specific goals and identifying strategic indicators and measures. The complete sustainability programme will be part of the next sustainability report.
List of material topics
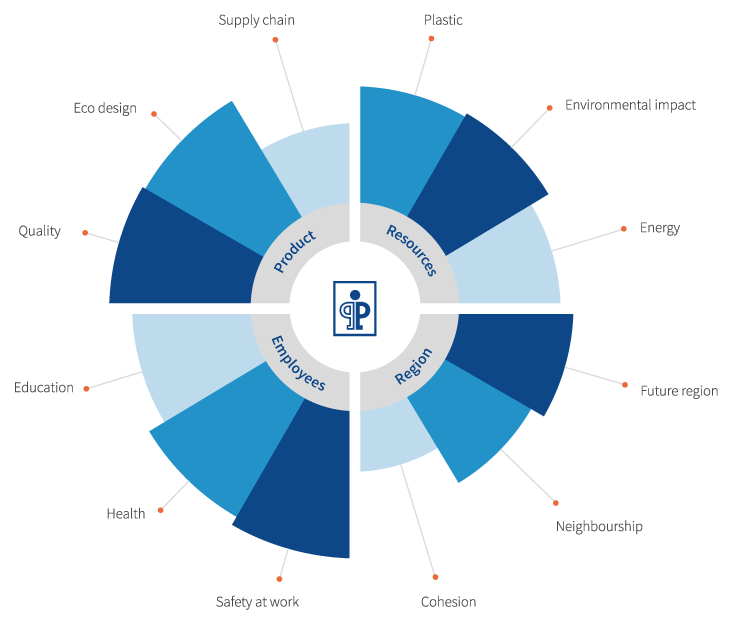
This is our first GRI report. This information is therefore not applicable for us.
This is our first GRI report. This information is therefore not applicable for us.
The data and information in this report refer to the 2017 and 2018 financial years.
This is our first sustainability report created in accordance with the GRI standards. We plan to publish further reports every two years.
For questions or comments regarding the report, please contact nachhaltigkeit@poeppelmann.com. The main contact person is Benjamin Kampmann.
We have created this report in accordance with the GRI standards with the “core” option.
The executive board has decided to subject the information in the GRI index to an external review. We expect this to increase the credibility and quality of our information. To review the information, we have chosen the independent environmental expert and specialist organisation ENVIZERT GmbH (Borkener Straße 68, 48653 Coesfeld), which also audits our environmental and energy management. The test report can be accessed online in German.
GRI 200 ECONOMIC STANDARDS
As a plastics processing company, we develop, produce and sell a wide range of products in various markets across the globe. We predominantly supply the automotive and electrical industries, commercial horticulture, medical technology and the packaging and food industries. All of these sectors are important and cover the basic needs of modern people: medicine, nutrition, mobility.
Quality plays a central role here. After all, our products must be safe, environmentally friendly and as innovative as possible in order to meet the growing social demands and the ever-increasing market requirements. And all this at a fair price. This is only possible with a meticulously honed quality management system that focuses on the overall organisation and is closely interlinked with other management systems.
Policy and organisation
We introduced our quality management systems back at the beginning of the 1990s and have continuously developed them since then. Over the years, an integrated management system has emerged. Today’s management system combines the areas of occupation safety, the environment, energy, quality, risk management and compliance with the aim of efficiently implementing the system requirements throughout the entire organisation. The application area spans the divisions FAMAC®, KAPSTO®, K-TECH®, TEKU®, WTZ and CP Holdorf.
The executive board assumes overall responsibility and accountability for the management system. However, all staff members are responsible for compliance with requirements and continuous improvement in their area. The management manual for quality, occupational safety, environmental protection and energy seamlessly fits into the comprehensive process landscape of the Pöppelmann Group and enables a holistic view of the company.
We want to achieve consistent and predictable results effectively and efficiently in our day-to-day work. This is why we use the ‘process-oriented approach’. This facilitates alignment concerning the development, implementation and constant improvement of the management system and promotes the fulfilment of customer requirements. The process-oriented approach taps into the structure of company processes and enables a clear representation of the reciprocal effects of individual sub-processes as a process landscape. Here, we differentiate between four process levels: management processes, value creation processes, supportive and supported processes.
In the individual divisions, a quality management system has been implemented in accordance with various system standards. The alignment follows the respective market requirements.
• In the Division KAPSTO®,a process-oriented quality management system as per DIN EN ISO 9001:2015 is used. This spans management, value creation and supportive processes and other supported processes for the subsidiaries PPUSA and PPF. The requirements of interested parties are taken into consideration.
• The K-TECH® division has implemented a quality management system in accordance with IATF 16949:2016 which, alongside management, value creation and supportive processes, also includes further processes for the subsidiaries Pöppelmann Plastics USA LLC and Plastiques Pöppelmann France S.A.S.
• The basis of the quality management system implemented in the FAMAC® division is DIN EN ISO 9001:2015, which we expand further based on the requirements of BRC Packaging (Version 5). We have also integrated DIN EN ISO 13485: 2016 in the management system for the medical products area.
• The quality management system in the TEKU® division also follows a process-oriented approach based on the systematics of DIN EN ISO 9001:2015. The complexity of the design is aligned to the requirements of the market with the aim of providing consistent products and services that meet customer expectations and legal and regulatory requirements.
Communication and employee involvement
Ensuring that all of our employees identify with the company and our objectives is a fundamental concern for us. This is why open and honest communication and socially responsible and ethically correct conduct are a matter of course for us. We believe that the high level of qualification and motivation amongst our employees plays a crucial role in our company’s success. We promote and encourage this commitment through a range of measures, including our training and education system, the PP Academy, the company newspaper and our ideas box. Other benefits round off the Pöppelmann standard.
Results and outlook
Over the past few years, we have dedicated continuous efforts to the improvement of our internal processes and increasing our productivity and quality. Last but not least, the further development of our management system better helpes to fulfil the increased requirements in all areas of the Pöppelmann Group and achieve the aim of sustainably oriented value creation and the associated increase in customer benefit.
We pay our employees above the statutory minimum wage. Remuneration primarily depends on employee function. Our salaries do not differentiate between genders.
All members of the executive board live with their families in Lohne or municipalities in the Vechta district.
As a company with deep roots in our home region, our responsibility does not end at the site gates. On the contrary, we want to help shape a strong region with our work. Our clear focus is on economic stability, good relationships with our neighbours and social cohesion. After all, strong companies need strong regions and vice versa.
Policy and organisation
In the decades since our foundation, the regional focus of our corporate policy has above all flourished in many personal relationships and has – at least up until now – been less shaped by strategic considerations.
We support regional suppliers and try to give them preference wherever possible under the same conditions. Through fair and competitive pay, we want to contribute to the consolidation of regional prosperity. As the largest local employer, this is a responsibility that has always been an inherent part of our self-image.
The same goes for our promotion of community and culture. In addition to the Industrial Museum and youth club in our home town of Lohne, which are among the most prominent examples of our social commitment, we support numerous other regional activities, measures and projects. So far, we have not adopted a structured approach in this area. Instead, we opt for organically developed relationships with various local communities.
Ultimately, we want to maintain good relationships with our neighbours. Our employees and their families are not only our residents and neighbours, but also part of other local communities. We therefore try to understand and respond to the concerns of our fellow citizens.
For example, our growth phase has also resulted in increased strain on the local infrastructure. This leads to traffic congestion, increased noise levels and higher emissions. This is why we are currently in the process of developing a modern infrastructure concept that will offer a solution for everyone involved.
Communication and involvement of local stakeholders
Good relationships are based on good communication. This is why we want to ensure that local stakeholders from politics, the economy and civil society are informed and involved even more in the future.
One example of this from the reporting period is the Citizens’ Dialogue carried out as part of the first Pöppelmann Researchers’ Sunday, which we held in collaboration with the Lohne Industrial Museum in November 2018. There, we explained working methods and technologies used in our industry and answered questions posed by members of the local community, including on controversial topics in connection with plastics processing. Through company tours, ‘Taster Days’ for school pupils and other events, we also strive to increase transparency and presence – a trend that is new for us, too. However, we feel good about this – after all, we see ourselves as an integral part of society. We will also seek dialogue with local environmental organisations, political and administrative bodies and other local companies to identify and promote important regional issues to ensure a strong region.
Results and outlook
We want to continue and build on our existing commitment and thus our contribution to the positive development of our region. In doing this, our activities place particular emphasis on dialogue with the local community.
We are one of the largest companies in the Vechta district and are the biggest employer in our home town of Lohne (Lower Saxony, Germany). As a result, our actions have direct and indirect effects on local communities and the regional economy. We see ourselves as part of the local community and understand this as a responsibility to make a contribution to social prosperity and cohesion.
We continuously support a number of voluntary associations and organisations in Lohne. Concerning our social commitment, we have defined two focus areas: we collaborate closely with Lohne Industrial Museum in the cultural and scientific fields on the one hand while actively promoting the social work of Lohne Youth Club on the other. In 1991, the Pöppelmann family gifted the company’s former headquarters in Bakumer Straße to the town of Lohne to be used for youth work.
In 1997, former managing directors Gertrud Pöppelmann and Karl-Heinz Diekmann provided the decisive impulse for the construction of Lohne Industrial Museum. Since its opening in 1987, it had been housed in a small building that used to be a carpentry workshop. When Gertrud Pöppelmann and Karl-Heinz Diekmann left their operational management posts in 1997, they declared that they would provide the construction financing for the long-planned industrial museum. In 2000, the museum opened in its new home opposite Lohne train station. Since then, we have closely accompanied the development of the museum into one of the region’s most important cultural hubs. To commemorate the industrial history of the Oldenburger Münsterland, it keeps alive the memory of the beginnings of the region’s business life and the work of the people who made it all possible. In November 2018, we collaborated with the museum team to organise the 1st Pöppelmann Researchers’ Sunday in the museum. With more than 1,000 visitors, the event served as a platform for dialogue on the subject of plastic, and met with a huge response from the public.
As one of the largest employers and taxpayers in the region, we make a significant contribution to prosperity and economic stability in the region.
From the total of approximately 15,000 workers in Lohne, we employ some 2,300 of them. With our fair remuneration, we ensure well-being in a region with above-average birth rates, high employment and a below-average long-term unemployment rate.
Alongside the direct effects, the indirect consequences of employment are also worth mentioning, which lead to an improvement of social conditions at many smaller regional companies with which we collaborate every day. A substantial number of our suppliers come from the region (Lower Saxony). We are proud to be contributing to regional stability in this way.
Educational migration is lower in Lohne than in the surrounding district of Vechta and the state of Lower Saxony. Our wide range of training and recruitment opportunities undoubtedly play a role in this (161 apprentices in 2018), which also give citizens with low qualifications long-term prospects in the labour market.
Approx. 18 % of the purchasing volume is placed regionally in Lower Saxony. This includes costs for electricity and gas, among other things.
Companies and all employees are required to comply with applicable laws, guidelines and internal regulations. The aim of the compliance management system is to systematically create the conditions in the organisation for employees to be shown a clear framework for action concerning internal and legal regulations. Management and advisory bodies are also supported in ensuring proper corporate governance and thus avoiding both damage to the company and personal liability of board members (advisory board, board of directors, executive board).
Policy and management system
The compliance management approach at Pöppelmann is based on the ISO 19600 and IDW 980 standards and is documented in a compliance manual. Alongside our own commitments, we see ourselves as an integral part of our customers’ supply chains. We aim to meet the increasing demands of customers, such as from the automotive or pharmaceutical industries.
The Compliance, Insurance & Risk Management department is responsible for this subject in our company. In organisational terms, it is located in the Finance management area.
Our compliance management system has been in place since 2018. We are continuously develop and update it to reflect current issues. At the time of its creation, it includes the following elements:
• Own code of conduct for sites in Germany, USA, France, UK and China with norms and rules of conduct
• Investment guidelines, which regulate the purpose and amount of expenditure and the investment procurement process
• Implementation of the General Data Protection Regulation (GDPR): Introduction of a legally compliant organisation and corresponding processes
• IT security regulations and project data classification
• Organisation Supplier Ethical Data Exchange (Sedex) – Smeta4Pillar Audit (since end 2014)
• Employer fiduciary duty: Travel Risk Management International SOS (ISOS)
• Complete re-structuring of customs/foreign trade organisation
Company management and the compliance manager operate a zero-tolerance policy when it comes to dealing with the violation of rules. Disciplinary action will be taken uniformly and consistently in the case of violations. All employees in the Pöppelmann-Group as well as all customers, suppliers and external stakeholders have the right to notify us of possible violations via various internal and external channels (e-mail, telephone or in person).
In order to secure and increase our sustainable success, we have implemented a holistic opportunity and risk management approach in accordance with ISO 31000 and IDW 981. Our active risk management creates transparency about opportunities and risks and supports the divisions in achieving their short-, medium- and long-term goals. In terms of competition, proof of an effective risk management system as a proactive part of our organisational processes serves as a decisive lever to gain or maintain the trust of our customers, suppliers and insurers.
Communication and employee involvement
Compliance is relevant to everybody, from apprentices to the executive board. The topic of compliance and risk management is on the agenda for all senior management, supervisor and division leader team meetings. Weekly meetings are held with the executive board, in which current and future compliance topics are addressed and developed.
During the reporting period, we have developed and implemented a training concept with special emphasis on data protection and security awareness. Some of the training courses were held on-site with external specialists and via e-learning modules. Approx. 700 employees completed the courses.
A comprehensive training concept will soon be drafted in collaboration with the executive board, which will present all employees with a clear framework for action.
Results and outlook
Our fundamental objective is to ensure that no legal violations are committed. These can have an adverse effect on the company, customers and suppliers. In addition, those involved should be given a clear framework for action in order to be able to carry out the corresponding tasks.
To date, we have not registered any incidents of corruption or failed audits. Various customer audits were carried out from 2017 to 2018. We carry out supplier audits at regular intervals.
The following points define a series of topics that are to be included in the future:
• Implementation of a multilingual, global compliance organisation for all business units
• Classification of compliance and corporate social responsibility (CSR) in the PPx management system
• External publication of the Pöppelmann Code of Conduct
• Benefits in kind: establishment of rules, limit values and approval processes for any benefits in kind (e.g. gifts, invitations, sponsorship, etc.) on the part of employees, customers and suppliers
• Publication of compliance manual
• Introduction of SAP GTS: development of our own compliance module for customs and foreign trade
• Internal control system for tax compliance
Funds are only released according to the dual-control principle. We are currently carrying out internal checks on subsistence and travel expenses. There are no internal compliance checks at the moment; coordination with the executive board is required.
Audits are initiated by customers: in particular, customers from the automotive area carry out compliance checks on us. In addition to environmental concerns, compliance with laws and human rights, corruption is an important issue. We also examine how such issues are communicated internally and how we can raise awareness of them amongst our employees.
No significant corruption risks were identified (see also GRI 205-3).
We have a purchasing conduct guideline for our employees to follow. Our subsistence and travel expenses guideline also partially regulate the issue of benefits in kind. Alongside the dual-control principle, event-related training courses are also offered depending on the area.
As part of regular meetings with the executive board, we have decided to develop a comprehensive compliance training concept for all employees. This aims to provide all employees with a clear framework for action concerning all important compliance aspects, such as corruption or cartels.
No incidents of corruption have been registered to date.
To date, we have not registered any legal proceedings due to anti-competitive behaviour, antitrust or monopoly practices.
GRI 300 ENVIRONMENTAL STANDARDS
As a plastics processing company, we see it as our duty to make our products and processes as environmentally conscious as possible. The topics of occupational safety, environmental protection and energy efficiency are firmly anchored in our corporate policy.
Policy and organisation
The company policy contains conduct guidelines with regard to environmental protection, energy efficiency, occupational health and safety and quality. These are defined by the executive board and updated as required. We are committed to protecting the environment and creating optimal working conditions. We want to operate sustainably, use resources sparingly, use energy efficiently and keep waste to a minimum. We maintain an integrated management system for the areas of environment, energy and occupational safety in accordance with the requirements of the EMAS regulation EC 1221/2009, DIN EN ISO 14001, DIN EN ISO 50001 and DIN ISO 45001. Within the EMAS framework, we have been openly communicating our environmental protection activities since 1996. In the annual environmental statement, we report on our environmental performance at our sites in Lohne and Holdorf (since 2017).
The executive board is responsible for this management system. It defines responsibilities and delegates tasks. The management representative is the technical director. He monitors the maintenance of the management system and ensures that corporate policy and objectives are implemented and the necessary funds are provided.
The occupational safety specialists and environmental protection and energy officers monitor the implementation of the requirements and advise employees and management. They manage the documentation and report annually on environmental performance and energy efficiency. They accompany the implementation of targets. The other legally required and voluntarily appointed officers contribute significantly to environmental protection through their specialist knowledge. They monitor the legal and internal requirements in their area and ensure that environmentally friendly technologies are implemented. They report to the executive board annually.
Cross-departmental topics are addressed in numerous committees, such as the safety and environmental committee and the energy team.
Communication and employee participation
The consultation and participation of our employees is of utmost importance to us. This is why we maintain open dialogue and include our staff members in all work processes. All of our employees are encouraged to actively participate in the further development of our management system. Instructions and further training measures ensure that they are qualified for environmental and safety related behaviour. All employees can access the management system documentation via an internal information system. Another tool for communication is our shop floor management, in which occupational safety and environmental protection come first.
In the annual environmental statement, environmental performance and energy related performance are communicated internally and externally. In it, we inform staff, the public and interested parties about the status of environmental protection.
Results and outlook
We want to improve continuously! We evaluate our performance based on environmental, energy and occupational safety indicators, for which we have set specific targets. In order to achieve these, we implement the required measures through the environmental program, which contemplates environmental, energy and occupational safety aspects. We evaluate the attainment of targets at regular intervals.
Our most important key figures include the rate of accidents at work, resource consumption (plastic consumption), the energy consumption rate, waste rate and the water consumption rate.
The effectiveness of the management system, its implementation in operations and compliance with legal requirements is assessed through internal and external audits. Audit results and performance data are reported to the executive board annually by the responsible departments and commissioned officers. These reports also serve as a basis for the evaluation of the management system by the executive board. If necessary, it defines the need for action for improvement and corrective measures in order to maintain and improve the management system.
In addition to the careful treatment of natural resources, the effective and efficient use of material is one of our focal points. Here, we concentrate on our most important material: plastic. This is why we are always looking for ways to reduce material consumption and close cycles. On the one hand, we want to ensure resource efficiency as part of our production processes. On the other hand, we go one step further and try to close cycles in order to protect resources on a systemic level.
Policy and management system
Resource efficiency is part of our environmental management system. To this end, we have set ourselves ambitious goals for our various sites, all of which are over 90 %. The aim of this is to keep the difference between material input and output as low as possible. For this purpose, we have implemented technical and organisational measures that we uphold every day.
From a strategic point of view, the proportion of recycled plastic is the second measure we pursue in the long term. This is relevant to us because it enables us to develop the potential of the circular economy.
At the beginning of 2016, we started to investigate the recyclability of our packaging in the TEKU® and FAMAC® divisions. After successfully closing the material cycle in the TEKU® division with the Circular blue plant pot, we have adopted this approach for products in all divisions. At the beginning of 2018, the PÖPPELMANN blue® initiative was launched, which will now shape both our daily activities and our future.
In short, the aim of PÖPPELMANN blue® is to close cycles. For us, a closed material cycle means that we procure raw material from a source that is also used for the disposal of an equivalent product by the user. For the plant pot, this means that it is made of material from the polypropylene category of ‘yellow bag’ household recycling, and can be disposed of after use in the ‘yellow bag’ household recycling because it is recognised as polypropylene and is thus returned to the polypropylene category.
All of our divisions implement PÖPPELMANN blue® projects independently. The divisions have notified the steering committee of target values for the years 2022 (target year for the current Pöppelmann strategy) and 2025 (target year for the EU strategy). The current status of the projects is presented at quarterly steering committee meetings. The steering committee is made up of five members of the group of shareholders, advisory board and executive board.
Communication and employee involvement
The regular steering committee meetings ensure that the divisions exchange information with each other and the central departments, such as purchasing and marketing. The topic is also conveyed to the workforce through reports in the company magazine and the ‘Plasticmobile’ apprentice initiative. In addition to this, a newsletter is published at irregular intervals, which is aimed at all employees and reports on current projects in all divisions.
Results and outlook
With the PÖPPELMANN blue® initiative, we have set ourselves ambitious targets until 2025. Three of these should be highlighted:
• Recyclability: By 2025, 100 % of the packaging we manufacture will be recyclable in accordance with the standards then applicable in Germany or the EU.
• Recycled material: In 2025, we will use at least 20 % recycled material from closed material cycles (based on our use of plastics in Germany).
• Material requirements: by 2025, we want to cover 60 % of our material requirements with recycled materials (including post-industrial recycled materials).
In the next report, we will be able to report on the advances of the PÖPPELMANN blue® initiative.
Plastic is our main material. In plants 1 and 3, we predominantly use the plastics polypropylene, polyethylene and polystyrene. In plant 2, engineering plastics like polyamide, polyacetale, polycarbonate, polyester and thermoplastic elastomers are also used.
Other materials required for our production process are cardboard boxes (2,688 tonnes) and plastic packaging (439 tonnes), which we need to protect our products during transport. We also use metals (76.89 tonnes) for tool manufacturing and mechanical engineering, as well as hydraulic oils (46.9 tonnes) to operate our production machines.
The plastic input remained constant during the reporting period. In 2018, it was 67,034 tonnes. As part of our production expansion, quantities have increased by approximately 20 % from 54,102 tonnes (2014) over the past five years. Especially in plant 3, the input increased significantly due to the construction of an additional production hall with new production facilities.
Input plastics [t]
Plant | 2014 | 2015 | 2016 | 2017 | 2018 |
---|---|---|---|---|---|
Plant 1 | 40,572 | 40,297 | 39,960 | 42,421 | 41,141 |
Plant 2 | 6,682 | 7,131 | 7,579 | 8,065 | 8,684 |
Plant 3 | 3,292 | 2,741 | 5,024 | 11,742 | 12,474 |
CP plant | 3,556 | 4,567 | 4,665 | 4,935 | 4,735 |
Total | 54,102 | 54,736 | 57,228 | 67,163 | 67,034 |
Our use of raw materials has been significantly increased during the same period. In plants 2 and 3, we are approaching the 90 % target we have for 2020. In plants 1 and CP, we have already exceeded 95 %.
Raw material efficiency [%]
Plants | 2016 | 2017 | 2018 | Target 2020 |
---|---|---|---|---|
Plant 1 | 97.6 | 98.7 | 98.7 | 98.0 |
Plant 2 | 86.9 | 86.4 | 86.5 | 90.0 |
Plant 3 | 81.6 | 86.3 | 87.0 | 90.0 |
CP plant | 97.8 | 95.4 | 95.1 | 98.0 |
We are continuously working on further optimisation in order to achieve our environmental goals. For instance, we are ensuring the efficient use of materials by reducing the wall thickness of our products and material recovery on production machines.
For each plant, we define the average recycling percentage of plastic components produced. The proportion of recycling in plant 1 is 71.9 %. We aim to increase this to 75 % by 2020. In plant 2, the recycling proportion if 13.7 %. No recycled plastic is processed in plant 3 since legal and customer requirements do not generally allow this for medical, pharmaceutical and food products. Nevertheless, we are also initiating our first projects here for the use of recycled materials in packaging. The recycling rate is already 100 % in the compounding plant.
In 2018, we launched the company-wide PÖPPELMANN blue® initiative, which is based on the concept of a circular economy. It makes provision for products to be manufactured from recycled plastics and aims to further increase the use of recycled materials at Pöppelmann. Through this, we want to close material cycles on one product level. This means that the material is taken from a used product and recycled to make a comparable product.
Each one of our divisions implements its own PÖPPELMANN blue® projects independently. The first products we launched were the TEKU® Circular blue plant pots in 2018. The plant pots are designed to ensure the reliable identification of the material by waste-sorting systems, thus enabling its use as new Pöppelmann PCR granules. In this case, the PCR granules are obtained entirely from household kerbside recycling (yellow bag and yellow bin).
We operate an integrated management system for the areas of the environment, energy and occupation safety.
learn more
We need energy to manufacture our products. With a share of between 85 % and 96 % of the total energy consumption, electricity is the most important form of energy in all plants. Other energy sources are gas for our building heating and fuel for our vehicle fleet. Until now, the fuel we use has been obtained exclusively from non-renewable sources. We do not generate energy that is sold. The amount of energy used in MWh is calculated from the consumption of electricity, gas and fuels.
Energy consumption [MWh]
Plants | 2014 | 2015 | 2016 | 2017 | 2018 |
---|---|---|---|---|---|
Plant 1 | 60,244 | 60,810 | 59,666 | 56,830 | 57,122 |
Plant 2 | 18,529 | 18,987 | 20,293 | 21,129 | 23,872 |
Plant 3 | 9,920 | 9,847 | 15,721 | 23,346 | 25,559 |
CP plant | 1,444 | 1,598 | 1,680 | 1,767 | 1,805 |
Total | 90,137 | 91,242 | 97,360 | 103,072 | 108,358 |
Our most important figure is the energy consumption rate. The energy consumption rate is the ratio of the absolute energy consumption to the material used on-site. In light of the various products and different manufacturing processes, the energy consumption rates of the four locations cannot be directly compared.
Energy consumption rate [MWh/t]
Plants | 2014 | 2015 | 2016 | 2017 | 2018 |
Target 2020 |
---|---|---|---|---|---|---|
Plant 1 | 1.48 | 1.51 | 1.49 | 1.34 | 1.39 | 1.45 |
Plant 2 | 2.77 | 2.66 | 2.68 | 2.62 | 2.75 | 2.60 |
Plant 3 | 3.01 | 3.59 | 3.13 | 1.99 | 2.05 | 2.50 |
CP plant | 0.41 | 0.35 | 0.36 | 0.36 | 0.38 | 0.35 |
In 2018, the energy consumption (MWh) for process and hall cooling increased in all locations due to significantly higher outside temperatures.
Plant 1: despite a 3.02 % decrease in material throughput compared to the previous year, the energy consumption rate in plant 1 rose from 1.34 to 1.39 MWh/t.
Plant 2: production started with new machines in hall 41. The base load of the hall for mould cooling, heating and air conditioning has had an effect on the increased energy consumption. The energy consumption rate increased from 2.62 to 2.75 MWh/t.
Plant 3: higher energy consumption was recorded at the plant. We attribute this to the higher energy consumption of the air-conditioned production halls and clean rooms in the summer months. For example, with approx. 1,485 MWh, the ventilation system in hall 33 consumed around 22.35 % more electricity than in the previous year. The energy consumption rate therefore rose slightly from 1.99 to 2.05 MWh/t of plastic.
CP plant: a second compounding plant was commissioned at the CP plant. As a result, energy consumption increased at the site. Since the plant was still in the trial stage and had not yet reached its full performance capacity, the energy consumption rate rose slightly. We expect an improvement in the energy consumption rate through the better utilisation of our plants in the future.
As a company, we strive to achieve a permanent reduction of our energy consumption. Due to strong company growth in recent years, our absolute energy consumption has increased compared to previous years.
In 2017, we set our strategic energy goals to be achieved by 2020, with 2017 as the base year for the strategy. This considers the forms of energy electricity, gas and fuel. The specified values are all measured and the fuel consumed is converted accordingly (see GRI 302-1). As part of the plant development, the energy base changed and the goals were partially achieved. It is therefore also necessary to adjust the goals next year (2020 for EMAS revalidation).
In order to achieve the strategic goals and continuously reduce energy-related performance, we run an energy programme, through which we pursue our operational objectives (e.g. improvement of energy monitoring, minimisation of thermal radiation losses, reduction of energy consumption for lighting). We monitor our processes and develop new measures through internal audits, monitoring key figures and regular plant inspections.
Energy consumption
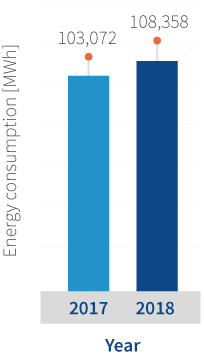
Water and wastewater are crucial environmental aspects that we consider within the context of the environmental management system. We procure fresh water from the public water supply provided by Oldenburgisch-Ostfriesischen Wasserverbandes. We do not currently use our own wells, despite having a permit for a restricted flow rate. Much of our water consumption is the result of evaporation in the cooling plants. Consumption is therefore weather-dependent and increases with rising outside temperatures, such as during the hot summer of 2018.
Unfortunately, today’s technical framework limits the possibilities we have to significantly reduce our water consumption. Nevertheless, we have also set a target for specific water consumption at each location in order to protect valuable drinking water reserves. Specific measures like renovating the cooking plants and more economical pump control are examples of our activities in this area.
Water consumption [m3]
Plants | 2014 | 2015 | 2016 | 2017 | 2018 |
---|---|---|---|---|---|
Plant 1 | 53,613 | 50,816 | 52,139 | 46,737 | 44,079 |
Plant 2 | 15,376 | 11,542 | 13,501 | 14,866 | 18,071 |
Plant 3 | 7,149 | 7,006 | 11,565 | 17,749 | 21,703 |
CP plant | 1,642 | 1,406 | 1,588 | 1,788 | 2,160 |
Total | 77,780 | 70,140 | 78,793 | 81,140 | 86,013 |
As with all key figures, the values of our four plants differ considerably: plant 1 consumed approx. 2,700 m³ less water. The water consumption rate remains unchanged because less raw material was used.
Due to the commissioning of hall 41, water consumption in plant 2 increased by approx. 3,300 m³. The rate increased from 1.8 m³/t to 2.1 m³/t.
In plant 3, water consumption rate also increased by 0.2 m³/t to 1.7 m³/t. Water consumption is around 4,000 m³ than the previous year. Production hall 33 now has significantly more production machines than in the previous year. The move from hall 10 is complete and the new equipment has been commissioned.
The addition of a second extruder, which was commissioned in autumn 2018 in the CP plant, has resulted in an increase in water consumption from 1,790 m³ to 2,160 m³.
Water consumption is determined using water meters and the quantity of evaporated water in the cooling towers is calculated.
No water sources are currently significantly affected by Pöppelmann’s water withdrawal. The over 2,500 measuring points in the Oldenburgisch-Ostfriesischer Wasserverband ensure that the quantity and quality of the groundwater comply with the regulations.
A total of 85 % of our fresh water requirements is required as cooling water for our technical systems. The cooling water is circulated as part of our production processes. It is reused until it has thickened three times and the salts contained in the water have reached a critical concentration. As a result, our current saving options under today’s conditions are exhausted, since further thickening would significantly increase consumption of water conditioning agents. This would also cause a disproportionate increase in corrosion and deposition problems. This process reflects the state of the art requirements. We also believe that the opportunities to influence water consumption are limited. Nevertheless, measures for the economical use of water are implemented, such as the renovation of cooling water systems and more economical pump controls.
Our plants border agricultural, commercial or residential areas. None of the plants that are the subject of this report border or are located in a protected area.
In the development of our products, we take relevant environmental issues into account and influence the life cycle under consideration of energy consumption, raw material consumption and disposal. We analyse the product life cycle and pay close attention to environmentally friendly product design. The use of energy-efficient, environmentally friendly product processes is particularly important.
As a plastics processor, plastic and microplastic pollution of the environment, especially the world’s oceans, is a key concern. Our approach is to prevent plastics from being released into the environment. We achieve this by using post-consumer recycled materials, which are recycled plastics made from used products. Through this, we help to ensure that plastic waste has a value and that more and more plastic is recycled.
To offset our land use in plant 1, we have an environmental compensatory area in the Roenbecker Possen corridor in Kroge, which measures 39,034 m². The area was created in accordance with the stipulations of the nature conservation support plan and is left to grow naturally. Other compensatory areas are defined by Lohne local council with the designation of industrial and commercial areas.
Compensatory measures are always carried out in agreement with Hase Wasseracht water board, Lohne local council and the responsible authorities. We do not work with any other third parties in this area.
Ecologically valuable areas on the company sites, such as restored streams, floodplain development, rainwater retention, etc. have the following sizes:
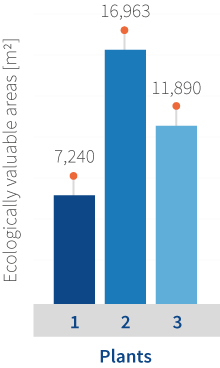
Our direct CO2 emissions (scope 1) come from the combustion of natural gas through the heating of buildings and the fuel consumption of vehicles. The reference year is 2017, the year of our last EMAS revalidation. In 2018, we produced 2,188 tonnes of direct CO2 emissions. This is an increase of 8.2 % compared to 2017 (2,022 t).
Direct GHG emissions (scope 1) [t]
2017 | 2018 | |
---|---|---|
CO2 from fuel consumption | 628.0 | 643.9 |
CO2 from natural gas consumption | 1,394.2 | 1,544.0 |
Total | 2,022.2 | 2,187.9 |
The conversion factors adopted from the EMAS programme only calculate the CO2-emissions directly generated during combustion. The conversion factors will be updated with the next EMAS revalidation.
Conversion factors: Petrol: 2,398 kg CO2/l; diesel: 2,618 kg CO2/l; gas: 1,879 kg CO2/m³
(Source: Swiss Agency for the Environment, Forests and Landscape, SAEFL)
Indirect CO2-emissions (Scope 2) are created during electricity production. In 2018, this was 38,324 tonnes. Compared to the previous year (40,307 t in 2017), we achieved a reduction of approx. 5 %.
Energy indirect GHG emissions (scope 2) [t]
2017 | 2018 | |
---|---|---|
CO2 from electricity generation | 40,307 | 38,324 |
In 2017, the proportion of renewable energies in electricity generation by our energy supplier was 39.2 %.
Other environmentally relevant emissions (scope 3) are of minor importance and are not currently recorded.
A key figure for us relates to the CO2-emissions (Scope 1 and Scope 2) per produced tonne of plastic – the CO2-intensity. As a result of our environmental and energy policy and the corresponding measures, the CO2-intensity has developed positively across all plants in recent years.
CO2-emissions per tonne of plastic [t CO2 / t]
Plants | 2015 | 2016 | 2017 | 2018 | Target 2020 |
---|---|---|---|---|---|
Plant 1 | 0.6 | 0.6 | 0.5 | 0.5 | 0.6 |
Plant 2 | 1.1 | 1.1 | 1.0 | 1.0 | 1.0 |
Plant 3 | 1.5 | 1.3 | 0.8 | 0.8 | 1.2 |
CP plant | 0.2 | 0.2 | 0.2 | 0.1 | 0.15 |
For the CO2-intensity, we have already achieved the goals of our environmental policy for 2020.
Overall, our absolute CO2-emissions (scope 1 and scope 2) have tended to increase in recent financial years, amounting to 40,512 tonnes in 2018. Compared to 42,329 tonnes of CO2 in 2017, the base year of the last EMAS revalidation, this equates to a reduction of approx. 4 %. However, compared to 37,369 tonnes of CO2 in 2015, this was an increase of around 8%. Despite the reduction in plant 1, values in plant 3 increased significantly in light of the construction and commissioning of the new production hall as part of our company development. The products manufactured in this plant also require special production conditions (ventilation and air-conditioning systems). The weather conditions (hot summer 2018) also contributed to this increase.
A positive development for us is that the CO2-intensity (see GRI 305-4), which relates to the amount of plastic processed, has been declining for years.
With minor deviations in individual plants, approx. 15 % of the fresh water is released as wastewater from sanitary water. The remaining approx. 85 % of water used is required for cooling purposes. The majority of this evaporates via cooling systems (60 % of total water), and the remainder (25 % of total water) flows directly into surface water under official requirements.
Effluents [t]
Plants | 2017 | 2018 |
---|---|---|
Plant 1 | 16.962 | 17.111 |
Plant 2 | 6.098 | 7.504 |
Plant 3 | 7.155 | 7.894 |
CP plant | 1.088 | 1.182 |
Total | 31.303 | 33.691 |
The direct discharge of cooling water into surface water is subject to official approval with requirements concerning the quantities introduced and compliance with limit values as specified in the Water Resources Law. No transgressions were identified during self-monitoring or official inspection by an independent laboratory in the last year. In addition to statutory requirements, we carry out weekly cooling water analyses.
As a waste generator, our company is responsible for the proper disposal or recycling of all waste produced. Our guiding principle is to avoid waste and recycle raw materials and resources. We work with specialist waste disposal companies, and place utmost importance on disposal safety.
According to the Circular Economy Act, we classify hazardous and non-hazardous waste. The waste generated at our sites is carefully separated according to an internal waste guide and disposed of following the waste hierarchy for proper waste recycling or disposal. All sites have collection points for waste and recyclables.
Non-hazardous waste:
In 2018, the amount of non-hazardous waste generated totalled 6,082 tonnes. This quantity has continued to grow in recent years, mainly due to our production growth. The waste rate (amount of waste per tonne of plastic used) is stable or diminishing in plants 1 or 3. In plant 2 and the CP plant, the waste rate has increased due to construction work and the associated waste.
Amount of non-hazardous waste [t]
Plants | 2014 | 2015 | 2016 | 2017 | 2018 |
---|---|---|---|---|---|
Plant 1 | 1,896 | 2,021 | 2,357 | 2,115 | 2,017 |
Plant 2 | 1,432 | 1,369 | 1,450 | 1,612 | 1,749 |
Plant 3 | 143 | 169 | 1,124 | 1,824 | 1,881 |
CP plant | 235 | 156 | 100 | 348 | 435 |
Total | 3,706 | 3,715 | 5,031 | 5,899 | 6,082 |
Non-hazardous waste rate [%]
Plants | 2016 | 2017 | 2018 | Target 2020 |
---|---|---|---|---|
Plant 1 | 6.0 | 5.1 | 5.2 | 5.0 |
Plant 2 | 19.3 | 20.1 | 20.3 | 20.0 |
Plant 3 | 22.4 | 15.5 | 15.2 | 20.0 |
CP plant | 2.5 | 7.5 | 9.4 | 2.5 |
Hazardous waste:
We consistently reduced hazardous waste in all sites by 2017. The large increase in hazardous waste in plant 1 during 2018 was the result of industrial flooring renovation work. This renovation work had a significant effect on the total amount of hazardous waste and the hazardous waste rate for plant 1.
Amount of hazardous waste [t]
Plant | 2014 | 2015 | 2016 | 2017 | 2018 |
---|---|---|---|---|---|
Plant 1 | 62.0 | 37.0 | 43.5 | 33.5 | 107.6 |
Plant 2 | 35.0 | 16.0 | 14.4 | 9.8 | 11.8 |
Plant 3 | 9.0 | 5.0 | 3.4 | 0.9 | 10.4 |
CP plant | 24.7 | 14.6 | 18.6 | 14.5 | 6.8 |
Total | 130.7 | 72.6 | 79.9 | 58.7 | 136.6 |
Hazardous waste rate [%]
Plants | 2016 | 2017 | 2018 | Target 2020 |
---|---|---|---|---|
Plant 1 | 1.8 | 1.6 | 5.1 | 2.0 |
Plant 2 | 1.0 | 0.6 | 0.7 | 1.0 |
Plant 3 | 0.3 | 0.0 | 0.5 | 0.5 |
CP plant | 15.7 | 4.0 | 1.5 | 10.0 |
The disposal of waste – and especially hazardous waste – is only carried out by specialist waste disposal companies which also take care of its transport.
There is no international shipment of waste. The amount of hazardous waste is specified in GRI 306-2.
Environmental legal obligations predominately arise from the Federal Control of Pollution Act, the Water Resources Law and waste laws. In occupational health and safety, the Occupational Health and Safety Act, the Industrial Safety Ordinance and trade association regulations and information are of particular importance. Compliance with legal requirements is checked as part of internal and external audits. During the reporting period, no violations of environmental laws or regulations were identified.
When purchasing goods and services, we not only consider economic aspects, but also ecological matters such as energy consumption, operating supplies, raw material usage, waste, waste disposal, life cycle, disposal after use, etc.
The purchasing or operating technology department coordinates with the client to specify the requirements for the goods, systems and services to be procured and, when placing the order, checks whether the required environmental and safety criteria are met.
The procurement of environmentally relevant substances is subject to special monitoring. In order to avoid a possible risk to people and the environment and to ensure compliance with legal stipulations, a process for the procurement and use of environmentally relevant and hazardous materials was introduced. The operational implementation is carried out through operating and work instructions.
Third-party companies that are contractually bound to our site are required to comply with the relevant safety standards as well as environmental regulations. Contracts signed by the organisation’s suppliers are inspected for completeness and compliance with the applicable legal provisions. The organisation attaches particular importance to the long-term, correct disposal of waste, since this is one of the company’s main environmental impacts. As part of the Circular Economy Act, priority is given to the safety of waste disposal in collaboration with the specialist waste disposal companies.
The environmental standards we demand of ourselves must also be fulfilled by our partners. The purchasing department is responsible for assessing suppliers. Evaluation is based on delivery performance (quality) and delivery reliability (quantity, date). Suppliers are also asked about the implementation of an environmental management system. This information should always be collected from new suppliers. Currently, we are not able to assess whether this is the case.
Overall, we have proof of a certified environmental system (acc. to DIN EN ISO 14001 or EMAS) for approx. 46 % of our active suppliers of goods and approx. 9 % of our active suppliers for services. We are currently expanding the systematic recording of supplier certification, which will enable us to specify the proportion of suppliers with a certified environmental management system in the future. Other suppliers are guided by established standards, but are not certified for various reasons (e.g. size of company). With the provision of the same quality and taking economic considerations into account, suppliers with the highest environmental standard are preferred.
GRI 400 SOCIAL STANDARDS
As an industrial company in continuous shift work, it is very important to us to offer above-average working conditions, which we enhance with additional voluntary social benefits. This includes aspects such as adequate remuneration, fair employment contracts and work/family reconciliation. We see this as the foundation of trusting collaboration.
Policy and organisation
Our general strategy is derived from the PPx principles adopted in 2017. On the basis of this, we have developed an internal strategy with goals and measures that are constantly reviewed and adjusted.
An important pillar of our strategy is long-term planning security. A total of 81 % of our employees in the three plants have permanent contracts. We cooperate with local companies for assembly work and use seasonal temporary workers to respond to order peaks. A condition of such collaboration is contractual assurance that all legal requirements, such as the minimum wage, are met. This enables us to avoid having to rely on contract workers and leased labourers.
The working hours of employees are recorded in working time accounts and can be flexibly structured within the framework of legal regulations. Striking the right balance between work and family has always been of huge important to us.
Communication and employee involvement
Members of our works council actively help to shape the framework conditions for our work and act as committed negotiating partners for management. Twice per year, management is required to report at a meeting convened by the works council.
Results and outlook
In light of the relatively recently established PPx corporate policy, we are unable to present any results for our current strategy. Regular analyses and assessments of personnel-relevant processes, key figures, programmes, audits and constant adaptation to new findings mean we can achieve the constant improvement of our management system.
During this decade, we have enjoyed steady growth, which is reflected in the steady increase in the number of our employees. In addition to apprentices, we have taken on a continuously growing number of new staff members in recent years. At the end of 2018, we registered 2,275 employees in Lohne and Holdorf. Since we also employ temporary workers throughout the year for seasonal and limited periods, information on employee recruitment can be misleading.
Employee turnover is almost exclusively attributed to moves to other employers. During the reporting years, a two-digit number of such cases was recorded. As proportions of the total number of employees for the reporting years, the values are 0.5 % (2017) and 0.6 % (2018). We see this as proof of our attractiveness as an employer and confirmation of our HR policy.
New recruits (total)
2017 | 2018 | |
---|---|---|
total | 357 | 485 |
of which male | 246 | 326 |
of which female | 111 | 159 |
under the age of 30 | 294 | 366 |
30 to 49 years of age | 55 | 109 |
50 years and older | 8 | 10 |
Employee turnover (total)
2017 | 2018 | |
---|---|---|
total | 208 | 287 |
of which male | 132 | 181 |
of which female | 76 | 106 |
under the age of 30 | 173 | 230 |
30 to 49 years of age | 14 | 27 |
50 years and older | 21 | 30 |
We are a family-run company and want to treat our employees as part of our family. In addition to adequate remuneration and statutory benefits, employees are given Pöppelmann Benefits, which can be divided into seven categories. Since this has grown into an extremely wide-reaching list, we have only detailed a few selected examples here. First of all, it is important to highlight that all of our staff are entitled to most additional benefits. We do not make a distinction between full-time and part-time workers or temporary and permanent employees, with the only exception being the BusinessBike offer.
1. Work and cohesion: events and celebrations for employees and pensioners; gifts and commemorative tokens for a range of occasions
2. Family, leisure and age: working time accounts; assumption of daycare fees and holiday care; extraordinary leave for special family occasions
3. Further training and development: assumption of costs for further training fees, PP Academy: wide prospectus of further training opportunities; learning workshop for our apprentices
4. Health and sport: company fitness programme with Hansefit and qualitrain; large range of preventative health courses; free natural remedies from the in-house PP pharmacy if needed; BusinessBike (only for permanent employees)
5. Nutrition: subsidies for company catering; home-made salads and muesli
6. Additional financial benefits: 100 % Christmas pay and 75 % holiday pay; bonus and special payments for various occasions
All of our employees are entitled to parental leave as far as is regulated by law. In 2018, 118 employees took parental leave, of which 83 were male and 35 were female. We are delighted to see more and more colleagues making use of this benefit.
Employees on parental leave
2017 | 2018 | |
---|---|---|
total employees | 100 | 118 |
of which male | 71 | 83 |
of which female | 29 | 35 |
No detailed information concerning employee return after parental leave is available at present. We will collect such data in the future and include it in the next sustainability report.
There are mutually agreed company arrangements between the employee representative body and the employer that also address this topic. Changes and renewals to these company agreements are made in close collaboration. As a family-run company, every individual is important to us. For this reason, we have taken unconventional paths and will continue to do so in the future.
At the height of the financial crisis in 2009, for instance, the executive board and works council reached an agreement to extend valid working time accounts at Pöppelmann. After overtime and the generally permitted time owed of 160 hours per person were exhausted, an additional 200,000 hours of time owed was distributed amongst the entire workforce in order to avoid redundancies.
We have not agreed any notice periods with the works council regarding terminations and closures. The current employment agreement includes an agreement on short-term work. With this, we aim to prevent redundancies during unfavourable business climates.
All existing employment agreements specify a period of notice. The statutory provisions apply to all other topics.
The mental and physical health of our staff is of paramount importance to us. By offering preventative services to maintain our employees’ ability to work, we assume social responsibility with the aim of reducing sick leave and increasing job satisfaction. Our employee benefits include a wide range of provisions that have a positive effect on the health of our staff.
Policy and organisation
The issue of health is assuming ever-increasing significance in considerations regarding our HR strategy. On the one hand, this is due to the rise in illness-related absences – a trend that can be observed throughout Germany. On the other hand, changes in working conditions such as increased workloads and increasing time pressure lead to new forms of stress for our employees.
Our occupational health management system consists of the three pillars occupational safety, occupational healthcare and occupational integration management. Although we do not have a classic company health management system, we are planning to expand and merge ongoing activities and measures.
Communication and employee involvement
The works council „Health & Safety Committee“ meets regularly and is involved in all considerations on how to improve employee health protection. Results and innovations are communicated both by the human resources department and the works council via notices and the company’s Intranet.
Results and outlook
In order to create a basis for this, we carried out an analysis of the current state. This shows a continuous rise in the illness rate despite a steadily decreasing accident rate. In order to react to this development, we have already implemented healthcare measures. This package of measures includes aspects of exercise, nutrition, medical care and mental health. During the reporting period, we also re-structured our company integration management. The goal is to overcome incapacity to work whilst preventing any new absences and enabling individual employees to keep their jobs.
Overall, we have set ourselves the goal of meaningfully linking and expanding our measures in the area of workplace health promotion and firmly anchoring the topic in the organisation.
We operate an integrated management system for the areas of the environment, energy and occupation safety.
learn more
In order to represent our entire workforce in the area of occupational safety, we have formed the Environment, Health and Safety Committee. This is made up of 33 members and regularly discusses, develops and implements measures for the improvement of occupational safety. Every quarter, it provides advice on prevention, risk reduction, corrective measures and workflow improvements. The executive board determines the group of participants. Alongside the executive board, the works council, company doctor and safety specialists, safety officers and managers from all sites also take part. The committee members are contact persons for our employees with questions and suggestions concerning occupational health, safety and environmental protection. Minutes are recorded along with a completion check.
Other committees are the works council Occupational Health and Safety Committee (8 people), the Kitchen Committee (7 people) and the Occupational Integration Management Committee (4 people).
As part of our occupational health and safety management system, we record key figures on accidents and illness rates. We analyse near-accidents, critical situations, work-related illnesses and accidents at work. The knowledge gained is incorporated into our risk assessments to enable the implementation of preventative, protective measures that sustainably improve the rates.
Overview of accidents at work
2011 | 2012 | 2013 | 2014 | 2015 | 2016 | 2017 | 2018 | |
---|---|---|---|---|---|---|---|---|
Accidents | 47 | 41 | 43 | 42 | 39 | 54 | 36 | 39 |
Accident rate* | 29 | 24 | 24 | 22 | 19 | 26 | 17 | 16,5 |
Days of absence | 422 | 359 | 440 | 469 | 395 | 534 | 399 | 420 |
Full-time employees | 1,641 | 1,715 | 1,833 | 1,949 | 2,045 | 2,080 | 2,080 | 2,366 |
Costs [€] | 128,288 | 102,755 | 133,760 | 187,600 | 161,600 | 213,600 | 159,600 | 191,600 |
In 2017 and 2018, the accident rate was 17 accidents at work per 1,000 full-time employees. In 2017, a total of 36 accidents were recorded and 399 days of absence across our four plants. In 2018, there were 39 accidents and 420 days of absence. The most common accidents for both 2017 and 2018 were hand injuries and cuts.
Our illness rate (proportion of illness-related absences in target working hours) was 4.6 % for 2018, which corresponds to an average illness duration of 12 working days. Assuming year-round employment, target working time attainment and deduction of a six-week holiday period, the absence rate for 2018 was 20 %.
Currently, we do not have any more detailed information. In the future, we will record such data to enable full disclosure in the next sustainability report in accordance with the new GRI 403-8 requirements (as of 2018).
Most Pöppelmann employees are non-union. We are not a member of any employers’ associations. The works council and human resources department collaborate on joint agreements, which are then presented to the executive board. In the event of specific questions, the works council consults the relevant trade union, although this is a rare occurrence in our everyday business.
Education is a core concern at Pöppelmann. Through training, we secure our specialists and managers of tomorrow. Further training opens up development opportunities and motivates people by imparting new knowledge and skills. Since the expertise and competence of our staff form the foundations of our success, we want to use our education and further training policy to promote and enable qualifications for everyone.
Policy and organisation
Training has always been extremely important to us. Every year, we train approx. 70 % of our apprentices in technical professions, 15 % in commercial occupations and a further 15 % as part of dual study courses. On 1 August 2019, we welcomed our 1,500th apprentice. Especially in view of the increasing shortage of specialist workers, we want to cover our personnel requirements with our own trainees. Around one third of our current staff completed an apprenticeship at Pöppelmann.
From their very first day with us, we emphasise just how important our apprentices and their work are to us. During the reporting period, there was a total of 160 young people learning their profession with us across all years. Their time at Pöppelmann starts with an introductory week, during which they are prepared for all aspects of work within the company. They learn about our PPx corporate policy and are informed of key rules, such as occupational safety requirements, find out about their apprenticeship timetable and visit all three Pöppelmann plants in Lohne. The week finishes with a two-day team-building event including an overnight stay. We also place great importance on the inclusion of our apprentices’ families. Parents of our new apprentices are invited to get to know our company and the trainers before the apprenticeships begin.
Part of the apprenticeship also involves various projects which, under the partial guidance of their trainers, are implemented by the apprenticeships themselves, such as the Plasticmobile initiative, company representation at training fairs and the annual Taster Days for school pupils. A highly qualified team of trainers, above-average remuneration and a committed youth and apprentice representative council round off the comprehensive package. For ten years, we have been offering graduates the opportunity to work as a trainee in various areas and processes. Our 24-month trainee programme has been offered in its current form since 2018. It was developed for technical and commercial graduates. Our eight current trainees are supported by a mentor and take part in a development programme. The aim of this is to offer them the best possible preparation for a position of responsibility in our company.
All measures in the area of further training are derived from our PPx-principles. We want our employees to develop further in accordance with their own strengths. Our PP Academy offers a wide range of events to all staff members. Some of the options are organised by target group or topic. With this, we want to enable colleagues to find courses that meet their needs. The PP Academy covers the development of personal, social, methodological and professional skills. Subjects not covered by the PP Academy can be chosen with external providers.
Communication and employee involvement
A separate specialist committee run by the works council represents the interests of employees in all matters concerning education and further training. The Education and Further Training Committee consists of four members of the works council and a representative of the youth and apprentice council (JAV).
Results and outlook
In order to give employees a better overview of courses and to enable them to find a suitable option to match their needs, we are currently developing an in-house digital training portal.
We employed 50 of the 62 apprentices who passed their exams in 2018. Most of the apprentices who left our company opted to continue their studies at college or university. We offered some of them the option to continue as student employees to enable them to work with us during semester holidays. This enables us to stay in touch.
So far, we have only recorded the number of participants for training courses. In 2018, 7,877 participants registered for internal and external training courses. The corresponds to an average of 3.5 events per employee during 2018. The average number of hours of further training per year, per employee and a breakdown by gender or employee category will be included in the next sustainability report.
Since 2010, we have been committed to enabling all employees to develop professionally. For this, we have launched programmes such as IT training, skills development, business training, first aid courses, health training, technical training and language courses. The seminars are given by internal or external speakers. Alongside these offers, our employees also have the opportunity to apply for cost sharing for further vocational training. In this context, Pöppelmann assumes up to 50 % of the costs incurred.
Overall, we significantly increased our investments in educational offers during the reporting period. The courses are attended by employees based on their individual requirements. The effectiveness of measures is assessed both by the employee and the respective manager by means of an evaluation form, which is first completed by the employee and then the manager.
The total number of training courses also includes obligatory instruction sessions. In the future, this information is to be recorded and specified separately.
Overview of employee development measures
Training courses 2017 | Participation 2017 | Training courses 2018 | Participation 2018 | |
---|---|---|---|---|
Pöppelmann Academy measures | 79 | 618 | 57 | 367 |
Measures outside of Pöppelmann Academy | 656 | 5,707 | 712 | 7,520 |
Total | 735 | 6,325 | 769 | 7,887 |
In order to facilitate the transition to retirement, all employees are given the option of taking partial retirement.
The current basis for the realistic assessment of strengths is an employee meeting with the respective manager. The concept of this discussion was extended in 2018 in accordance with our PPx-principles to include clearly structured and defined dialogue on strengths. From 2019, these employee-manager meetings are held once a year.
The protocol created as part of the strengths dialogue is only available to the employee and the manager and, for reasons of confidentiality, cannot be used as evidence that the strengths dialogue took place. We are currently looking at how we can systematically record and evaluate the implementation of the strengths dialogue in the future. We will provide an update on this in the next sustainability report.
We are a young company. Every second Pöppelwoman and Pöppelman are between the age of 30 and 50 and every third employee is under 30 years old. As a production company, it is hardly surprising that most of our employees are male. Nevertheless, we continuously strive to increase the proportion of female workers. In 2018, women made up one fifth of the workforce at our German sites. The proportion of female colleagues is much higher among younger employees.
Employee structure
2017 | 2018 | |
---|---|---|
Employees (total)* | 2,065 | 2,275 |
of which male | 1,651 | 1,801 |
of which female | 414 | 474 |
permanent | 1,770 | 1,842 |
of which male | 1,452 | 1,498 |
of which female | 318 | 344 |
temporary | 295 | 433 |
of which male | 199 | 303 |
of which female | 96 | 130 |
in full-time | 1,904 | 2,095 |
of which male | 1,635 | 1,777 |
of which female | 269 | 318 |
in part-time | 161 | 180 |
of which male | 16 | 24 |
of which female | 145 | 156 |
Agency workers | 0 | 0 |
Employee structure
2017 | 2018 | |
---|---|---|
Employees (total)* | 2,065 | 2,275 |
of which male | 1,651 | 1,801 |
of which female | 414 | 474 |
under 30 years of age | 690 | 779 |
of which male | 560 | 612 |
of which female | 130 | 167 |
30 to 49 years | 953 | 1,063 |
of which male | 778 | 874 |
of which female | 175 | 189 |
50 years and older | 422 | 433 |
of which male | 313 | 315 |
of which female | 109 | 118 |
Our control body, the advisory board, is made up of one female and four male members (see GRI 102-18). We cannot publish any information regarding the assignment of advisory board members to other diversity categories since this would enable connections to be made to personal data.
We have a zero tolerance policy concerning discrimination. For reasons of confidentiality, we have not established an official complaints office apart from the works council. With the help of an external provider, we have set up a hotline for all employees. They can use the hotline for various professional or personal issues, such as bullying or discrimination. To date, no incidents of discrimination have been registered and we have not had to take any remedial action.
We carry out a risk assessment of suppliers as required. We focus primarily on business variables such as liquidity, number of machines and systems and employees. For important aspects such as freedom of association and collection bargaining, we expressly refer to our code of conduct.
Since most of our suppliers are located in Europe, we also rely on the compliance of our partners with the regulatory requirements of their respective country. We operate a zero tolerance policy in this respect. We will stop working with any supplier who is suspected of violating such legal and international standards. We are not aware of any such cases to date.
We carry out a risk assessment of suppliers as required. We focus primarily on business variables such as liquidity, number of machines and systems and employees. For important aspects such as child labour, we expressly refer to our code of conduct.
Since most of our suppliers are located in Europe, we also rely on the compliance of our partners with the regulatory requirements of their respective country. We operate a zero tolerance policy in this respect. We will stop working with any supplier who is suspected of violating such legal and international standards. We are not aware of any such cases to date.
We carry out a risk assessment of suppliers as required. We focus primarily on business variables such as liquidity, number of machines and systems and employees. For important aspects such as forced or compulsory labour, we expressly refer to our code of conduct.
Since most of our suppliers are located in Europe, we also rely on the compliance of our partners with the regulatory requirements of their respective country. We operate a zero tolerance policy in this respect. We will stop working with any supplier who is suspected of violating such legal and international standards. We are not aware of any such cases to date.
We comply with the applicable regulations in our plants. In addition to internal monitoring, this is also checked in the annual audits for EMEA and DIN ISO 45001 recertification.
We carry out a risk assessment of suppliers as required. We focus primarily on business variables such as liquidity, number of machines and systems and employees. For important aspects such as compliance with human rights, we expressly refer to our code of conduct.
Since most of our suppliers are located in Europe, we also rely on the compliance of our partners with the regulatory requirements of their respective country. We operate a zero tolerance policy in this respect. We will stop working with any supplier who is suspected of violating such legal and international standards. We are not aware of any such cases to date.
We plan to conduct a human rights assessment next year.
The subject of human rights will become part of the planned training concept on compliance . This is intended to inform our employees about human rights due diligence. Since these training courses did not take place in the reporting period, we can only specify how many employees took part in these training courses in the next sustainability report.
We have two certified quality officers and internal auditors (1st party) in strategic purchasing who regularly accompany our certified supplier auditors (2nd party) from quality management to visit our suppliers to check that our standards and requirements are being met. However, we assess the existence of a certified environmental management system as part of the supplier evaluation. Those who cannot prove the existence of a corresponding system will receive a lower rating. For new suppliers, compliance with standards should generally be assessed based on existing certification. In individual cases, for instance if certification is not available, on-site audits will be carried out. We do not currently record any data that can be used to assess how high the actual proportion of evaluated new suppliers is. We aim to make a specific statement on this in the next sustainability report. We also asked our TOP 20 suppliers for purchased parts to complete a CSR questionnaire (environment, safety, compliance).
As of the time of reporting, we have not registered any breach of privacy or loss of customer data.
As of the time of reporting, we have not registered any cases of non-compliance with laws and regulations in the social and economic area.