Thermoforming with IML: the benefits at a glance.
- Material savings: Compared to injection moulding, thermoforming uses less plastic. Cups are significantly lighter (savings of > 25% are not uncommon).
- Maximum recyclability: Cup and in-mould label are made of the same material (polypropylene) - cups are very easy to recycle as mono-material packaging.
- High-quality decoration thanks to in-mould labelling: the label is an integral part of the packaging, resistant to moisture and temperature.
- Standard range with different sizes: no need to invest in customised moulds.
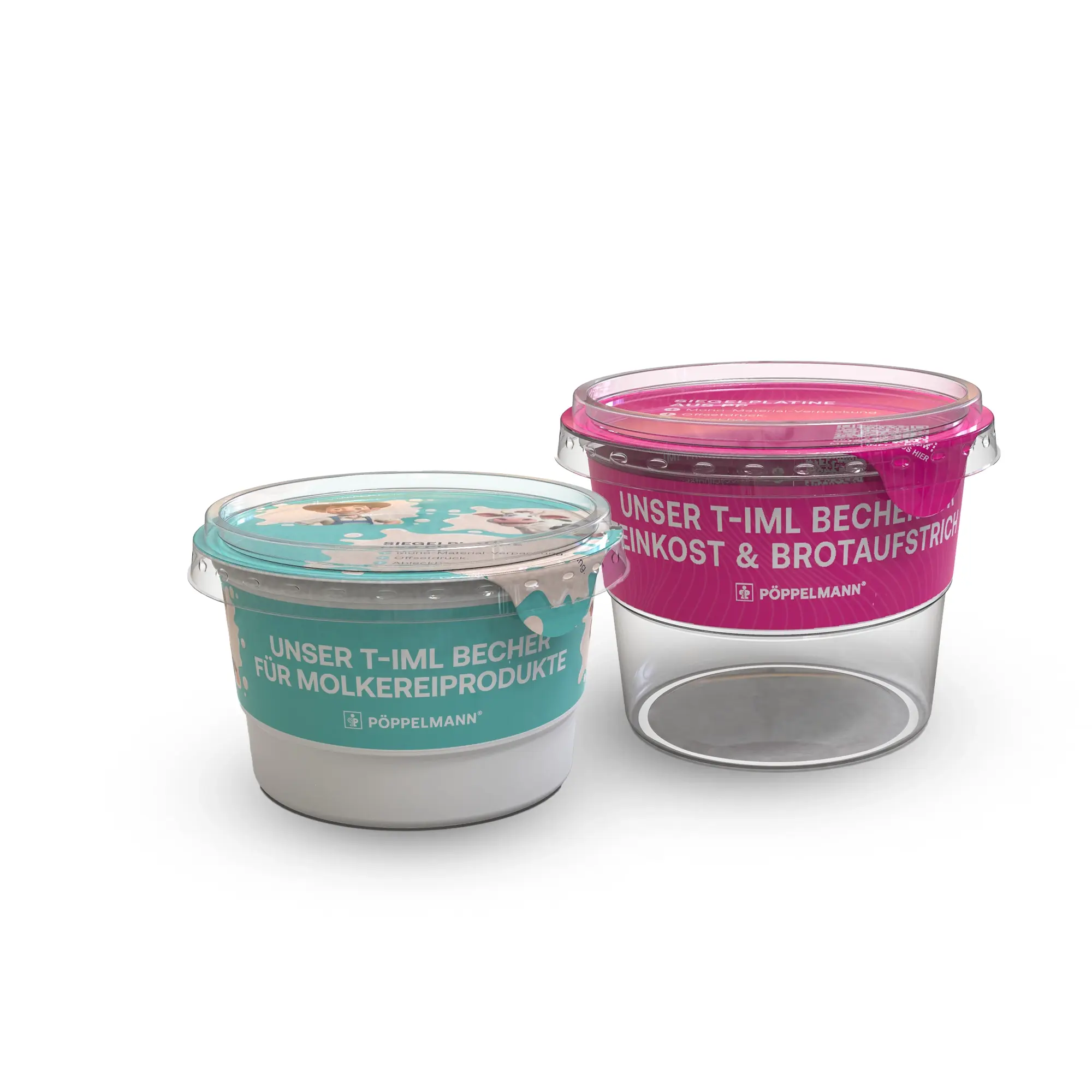
BDT Series | Thermoformed cups with In-Mould-Labelling in detail.
Plastic packaging contributes to CO₂ reduction because it is particularly lightweight. Resource-conserving product designs and efficient production processes can reduce material use even further. Our T-IML packaging minimises the use of materials.
The right cups for your product are available in different sizes - all sizes use the same lid.
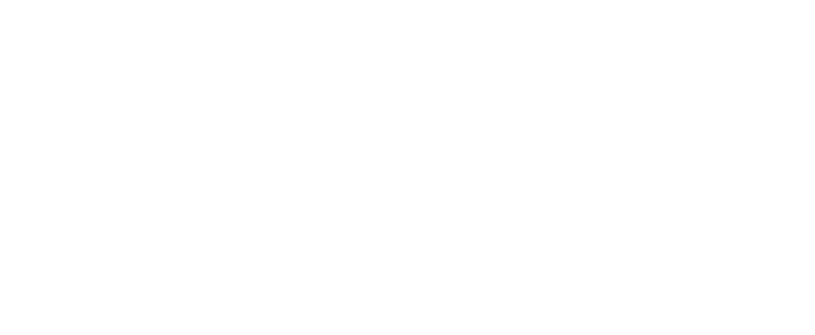
Standard colours: white, clear-transparent
Standard material: PP
Round Container
Order No. | ⌀ D1 mm | H1 mm | Capacity ml | IML In-Mould-Labelling | packaging unit |
---|---|---|---|---|---|
BDT 001-220 IML | 95,00 | 44,40 | 220 | x | 12.969 |
BDT 001-270 IML | 95,00 | 56,50 | 270 | x | 12.573 |
BDT 001-320 IML | 95,00 | 70,10 | 320 | x | 11.880 |
Snap-on Lid
Order No. | ⌀ D2 mm | H2 mm | Function | IML In-Mould-Labelling | Packaging Unit |
---|---|---|---|---|---|
D-BDT 003 SL | 98,60 | 13,65 | Snap-on lid | - | 16.368 |
What is thermoforming with IML?
In-mould labelling (IML) is the process of applying a pre-printed plastic label to plastic packaging during production. A robot positions the printed, thin plastic film in the mould. After the production process, the label and the moulded part form an inseparable unit with a continuous surface.
This decoration process is therefore the ideal basis for mono-material packaging. As the base material for the label and the plastic part is the same, IML-decorated articles are easy to recycle.
Until now, this technology has only been used for injection-moulded plastic packaging. We have combined our many years of experience in IML and thermoforming to produce a thermoformed milk tub using IML. The innovative and efficient T-IML process makes it possible to produce cups that are very light, because less plastic is used, and at the same time have a high-quality decoration.
Extremely lightweight.
T-IML packaging contributes to CO₂ reduction because it is particularly lightweight. When this advantage is combined with the use of recycled material, high recyclability and environmentally friendly production conditions, the reduction can be maximised.
Mono-Material.
The item and label are made from the same basic material, so the packaging can be easily recycled after use.
This is the basis for a circular economy.
Optimised Logisitics.
Optimising the article design has a positive effect on the stackability and nestability of cups, trays and lids. The quantity per packaging unit is maximised.
Optimised nestability ensures additional savings throughout the supply chain.
Test without obligation: Round cups from the FAMAC® T-IML programme.
Request samples of our packaging for testing - free of charge and without obligation.
Fill in the form now to receive a sample range.