We have expanded our cleanroom capacities.
Your advantages at a glance:
Plastic items for the pharmaceutical and medical device industries are subject to stringent cleanliness and hygiene requirements to ensure maximum product protection and user safety. By investing in a new cleanroom, we can now offer you even more options for manufacturing injection moulded products in a low-particle environment, such as large-format pharmaceutical packaging for the safe transport of glass and plastic syringes.
- Less particle sources, more safety:
The new cleanroom production generates less particle sources, from the injection moulding cell to the automated guided vehicles (AGV) and the automated packaging system. This enables us to offer even greater product protection and maximum patient safety in the manufacture of plastic products for the pharmaceutical industry and medical technology.
- Reducing greenhouse gas emissions:
By locating the machines outside the cleanroom, we reduce the energy required for ventilation and keep the energy consumption per square metre of production area as low as possible. This has a correspondingly positive effect on the reduction of greenhouse gas emissions from these cleanroom items.
- Expansion of clean room capacity:
The existing clean room of approximately 650m2 is now complemented by a modern and fully automated cleanroom of over 200m2, with the injection moulding machines located outside the cleanroom. The next phase of cleanroom expansion for assembly and finishing processes is already in the pipeline.
- Seamless quality management, certified cleanliness:
Our customers benefit from our many years of experience in the development and manufacture of plastic products, with corresponding documentation in line with the rules of GMP (Good Manufacturing Practice) - certified in accordance with DIN EN ISO 13485.
Would you like to find out more about the benefits of our new cleanroom?
Simply get in touch with us.
Book an appointment now!Highest quality and real climate protection:
Saving resources in practice.
When it comes to products for the pharmaceutical and medical technology industries, maximum product protection, maximum patent security and strict cleanliness and hygiene requirements are the top priorities. The way in which sustainable and resource-conserving plastic solutions can also be established in these areas is demonstrated by our cooperation with our customers Drägerwerk AG & Co. KGaA and QIAGEN N.V.
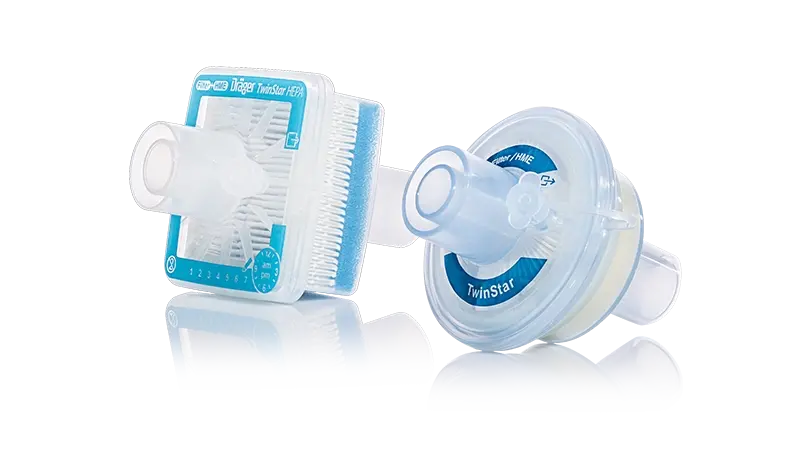
Respiratory system filters from Drägerwerk AG & Co. KGaA.

Reagent vessel from QIAGEN N.V.
All from a single source: from development to production
Whether for the laboratory or diagnostics sector, the pharmaceutical industry or medical technology, individual components or multi-part assemblies, packaging or functional parts. Since 2004, Pöppelmann has been producing FAMAC® plastic parts with special cleanliness and hygiene requirements.
Everything is supplied from a single source: from customer-specific development and tool manufacture to cleanroom production in line with GMP (Good Manufacturing Practice) regulations and corresponding documentation - certified in accordance with DIN EN ISO 13485.
Click here for more details!
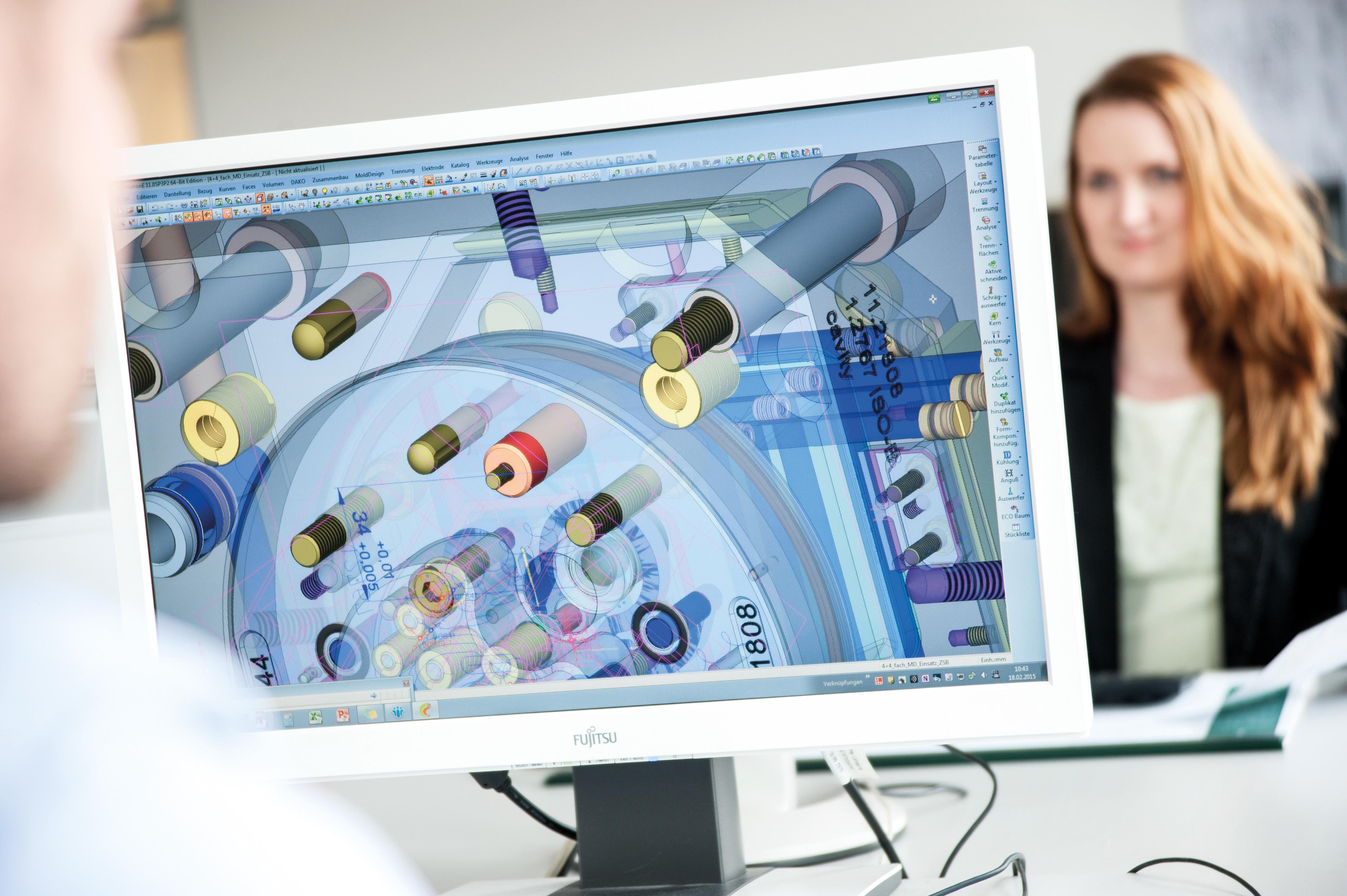
Certified safety:
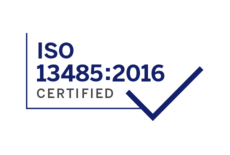
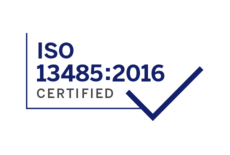
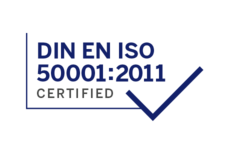
The advantages of quality management at a glance:
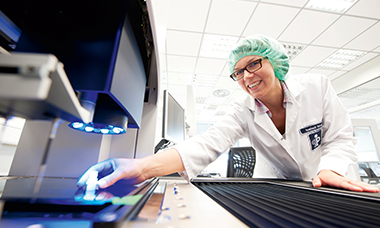
- Efficient: Incoming material inspection using thermal analysis (DSC).
- Cost-effective: Tactile and optical measurement using 3D measurement technology.
- Flexible: Three-dimensional measurement with GOM.
- Documented: In-process monitoring.
From development to series production: continuous quality assurance.
- Design Qualification (DQ): Development of a suitable tooling concept, taking into account the requirements from the specification.
- Installation Qualification (IQ): Completion of the tool and testing according to the requirements from the specification.
- Operational Qualification (OQ): Determination of a safe process window and verification of mould performance and machine capability.
- Performance Qualification (PQ): Determination and evaluation of the process capability of the plastic part.
