Mit Technologie vom Rohstoff zum fertigen Produkt.
Unser Anspruch ist es, qualitativ hochwertige Lösungen für Ihre Produkte zu entwickeln und diese effizient und wirtschaftlich umzusetzen. Dabei setzen wir auf Lösungen, die möglichst wenig Treibhausgase verursachen. Unser Ziel ist es, bis 2039 klimaneutral zu produzieren.
Wir scheuen keine Herausforderungen und gehen gemeinsam mit Ihnen immer wieder neue Wege: mit Hilfe eines eigenen Werkzeugbaus, modernsten Spritzgussautomaten, diversen Technologien, wie dem 2K-Spritzguss, MuCell® oder ortsgeschäumten PUR-Dichtungen (FIPFG) und Schweißtechnologien.
Spritzgießen.
Das Spritzgießen ist das meistverwendete Verfahren zur hochautomatisierten Herstellung von Werkstücken aus Kunststoff durch die Verarbeitung von Granulat.
Es lassen sich komplexe Formen, mit unterschiedlichen Oberflächen in nahezu beliebiger Größe erzeugen. Der Verarbeitungsprozess lässt sich vollständig automatisieren.
Dabei wird der Rohstoff in Granulatform aufgeschmolzen und unter hohem Druck in ein Spritzguss-Werkzeug eingespritzt. Nach dem Abkühlen kann der Artikel dann ausgeworfen oder mittels Automation entnommen werden.
Bei uns kommen im Wesentlichen Thermoplaste wie z.B. Polypropylen (PP) oder Polyethylen (PE) zum Einsatz.
Die Vorteile auf einen Blick:
- Gleichbleibende Qualität und hohe Produktionsleistung bei vorbildlicher Sauberkeit
- Schnell. Automatisierter Prozess.
- Materialvielfalt. Verwendung unterschiedlicher Materialien.
- Anspruchsvoll. Auch bei hohen Bauteilanforderungen einsetzbar.
- Prozesssicher. Vollautomatischer Fertigungsprozess, z. T. mit integrierter Prüfstation.
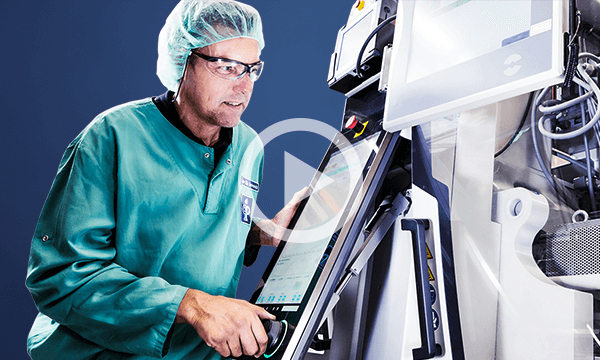
Zweikomponenten-Spritzguss für anspruchsvolle Multifunktionsteile.
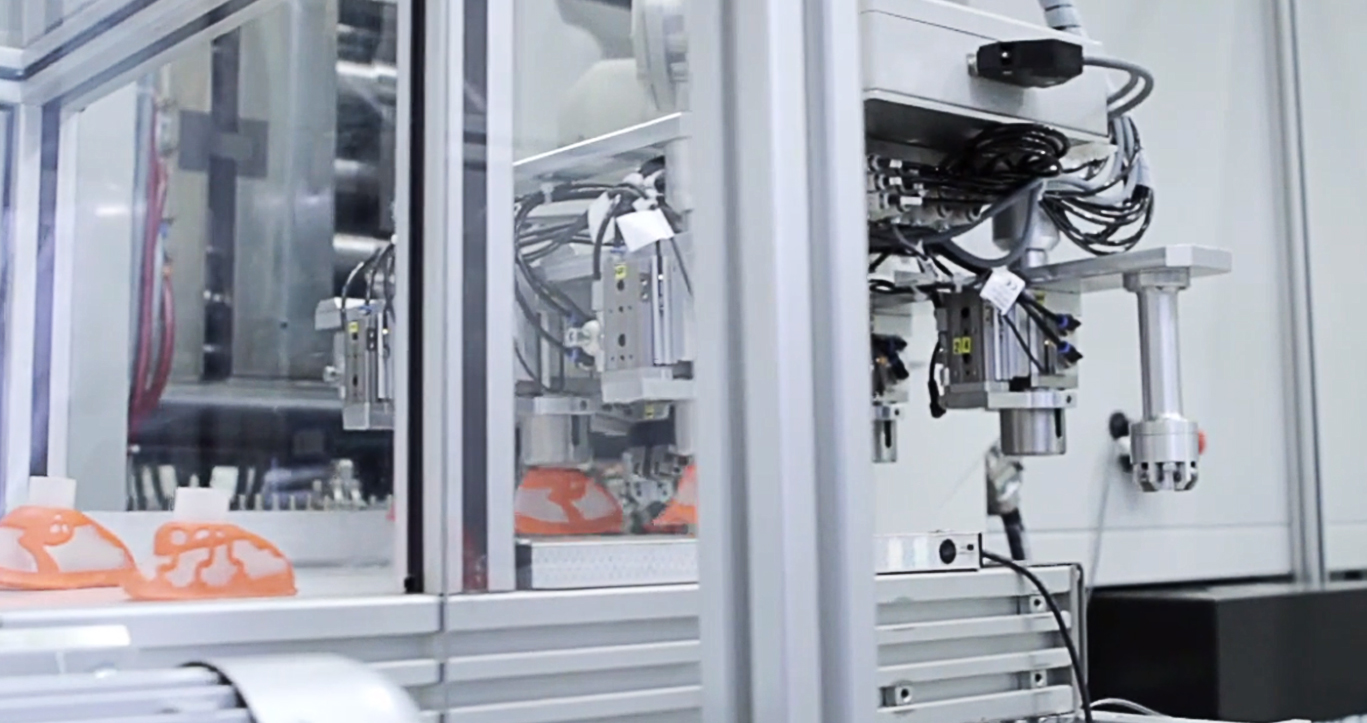
In 2K-Spritzgussteilen sind die Werkstoffeigenschaften von zwei verschiedenen Kunststoffen vereint. Außerdem sind mehrfarbige Teile herstellbar und selbst die formschlüssige Verbindung zweier nichthaftender Kunststoffe ist möglich. Daher kann ein einziges Bauteil eine Vielzahl von Anforderungen im Hinblick auf Funktionalität und Design erfüllen.
Dazu kommen wirtschaftliche und logistische Vorteile: Das Bauteil entsteht in einem Fertigungsablauf, sodass der Aufwand für Montage und Nachbearbeitung entfällt. Bei Pöppelmann sind alle Schritte von der Entwicklung des 2K-Teils über den Werkzeugbau bis zur Fertigung in einer Hand vereint. Mit diesem ganzheitlichen Konzept ist sichergestellt, dass 2K-Teile von Pöppelmann sich stets durch hohe Qualität und zugleich kostengünstig auszeichnen.
Die Vorteile auf einen Blick:
- Multifunktional. Unterschiedliche Materialkombinationen möglich.
- Prozesssicher. Vollautomatischer Fertigungsprozess z. T. mit integrierter Prüfstation.
- Wirtschaftlich. Ein Fertigungsschritt, zusätzliche oder nachträgliche Montageschritte entfallen.
- Dauerhaft. Feste Verbindung zwischen den Materialien.
- Anspruchsvoll. Auch bei hohen Bauteilanforderungen einsetzbar.
In-Mould-Labelling – hochwertig dekorierte Verpackungen.
Mit In-Mould-Labelling wird eine Kunststoffverpackung bereits während der Herstellung mit einem vorgedruckten Kunststoff-Etikett versehen. Dazu positioniert ein Roboter die bedruckte, dünne Kunststoff-Folie im Werkzeug. Dort wird sie fixiert und mit dem Behälter- bzw. Deckelmaterial hinterspritzt. Nach dem Spritzgießprozess bilden Etikett und Formteil eine untrennbare Einheit mit durchgehender Oberfläche.
Da Formgebung und Dekoration in einem Arbeitsgang erfolgen, entfällt der logistische Aufwand der Zwischenlagerung. Die ausgeprägte Zeit- und Kosteneinsparung machen den Einsatz des In-Mould-Labelling besonders wirtschaftlich. Zudem punktet das Verfahren auch unter Umweltaspekten. Bei gleichem Basiswerkstoff für Etikett und Behälter ist das Recycling von IML-dekorierten Tiegeln, Eimern, Kästen und anderen Verpackungen problemlos möglich.
Die Vorteile auf einen Blick:
- Präzise. Kein Verschieben und Verrutschen.
- Schnell. Automatisierter Prozess.
- Präzise. Vollautomatische Kontrolle mittels Kamerasystem.
- Wirtschaftlich. Formgebung und Dekoration in einem Arbeitsgang.
- Umweltfreundlich. Recycling bei gleichen Basiswerkstoffen.
- Hochwertig. Unverlierbarer Bestandteil einer Verpackung.
- Hygienisch. Feuchtigkeits- und temperaturbeständig.
Das Thermoform-Verfahren für ultraleichte Verpackungen und Trays.
Im Thermoform-Verfahren wird eine Kunststoff-Folie erhitzt und unter Vakuumeinfluss im Werkzeug in Form gebracht, abgekühlt und gleichzeitig ausgestanzt. Die dabei entstehenden Rechteckschalen und Rundbecher werden im Anschluss vollautomatisch aufgestapelt.
Das prozessbedingt entstehende Stützgitter wird dem Thermoform-Prozess als „neuer“ Rohstoff wieder zugeführt. Pöppelmann FAMAC® fertigt die dafür notwendigen Folien sofern möglich In-House.
Dank moderner In-Line- und Off-line-Lösungen produzieren wir unsere Artikel mit minimalem Materialeinsatz und erfüllen gleichzeitig die hohen Anforderungen unserer Kunden an Stabilität und Machinengängigkeit. Durch den geringen Materialeinsatz sparen wir Rohstoffe und reduzieren die Transportkosten entlang der gesamten Lieferkette.
Die Vorteile auf einen Blick:
- Ressourcenschonend durch geringen Materialeinsatz.
- Materialvielfalt durch In-House Folienproduktion.
- 40 Jahre Erfahrung im Thermoform-Verfahren.
- Gleichbleibende Qualität und hohe Produktionsleistung bei vorbildlicher Sauberkeit.
- Moderner Maschinenpark. Folienextruder sowie In- und Offline-Anlagen.
- Zertifizierung BRC.
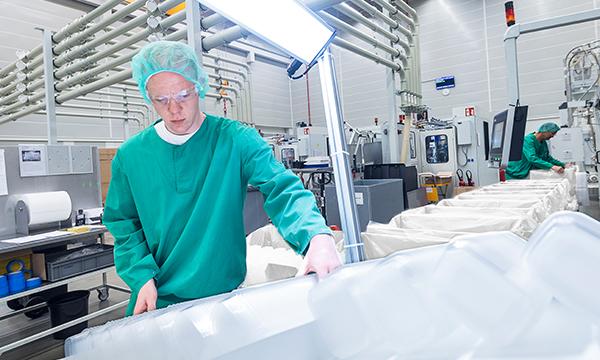
Reinraumproduktion – höchste, zertifizierte Sauberkeit.
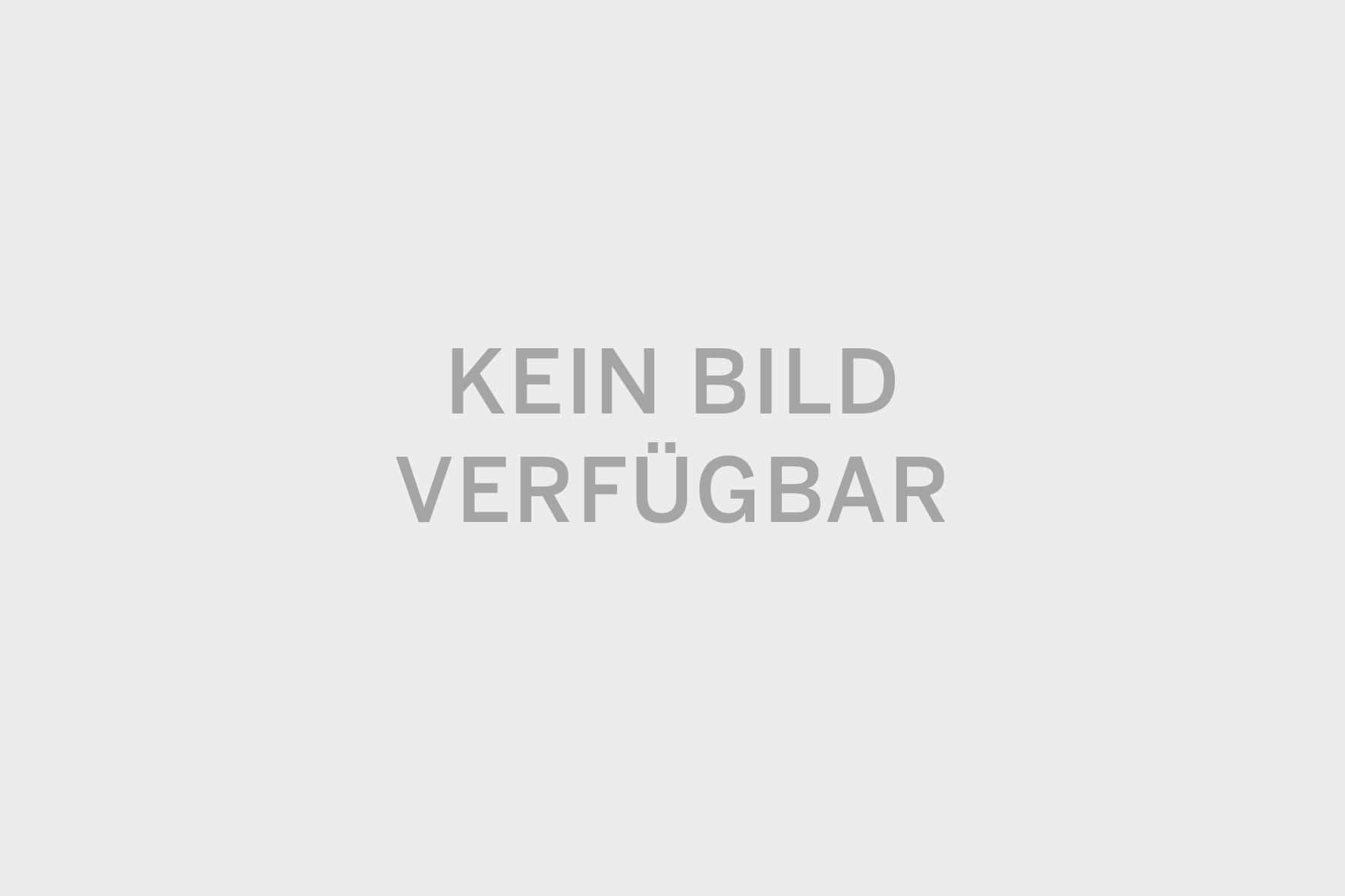
Kunststoffteile und -baugruppen mit höchstem Anspruch an die Sauberkeit werden bei Pöppelmann unter zertifizierten Reinraumbedingungen (DIN EN ISO Klasse 7, GMP Standard – C) gefertigt.
Die Spritzgussmaschinen einschließlich der Schaltschränke, Zusatzgeräte etc. sind außerhalb des Reinraums angeordnet, so dass die Wärmelast verringert wird. Dadurch sinken Leistungsbedarf und Betriebskosten der Klimatisierung. Nachrüstungen an der Maschine und spätere Erweiterungen sind ohne Beeinträchtigungen durchzuführen, so dass flexibel auf Kundenanforderungen reagiert werden kann.
Der außerhalb des Reinraums liegende Werkzeugbereich ist zum Werkzeugwechsel und für Wartungsarbeiten gut zugänglich, ohne die Abläufe im Reinraum und somit die Qualitiät der Kunststoffteile zu beeinflussen. Eine Havarie an einer Spritzgussmaschine oder einem Zusatzaggregat hat in der Regel keine Verschmutzung des Reinraums zur Folge.
Filteranlagen gewährleisten einen Partikel- und Keimanteil gemäß DIN EN ISO 14644 – Klasse 7 und Klasse C des EG-Leitfadens GMP, d. h. weniger als 350.000 Partikel/m3 bis herab zu einer Größe von 0,6 μm und weniger als 100 Keimbilder/m3.
Die Vorteile auf einen Blick:
- Sauber. Weniger als 350.000 Partikel/ccm (bis herab zu einer Größe von 0,6 μm).
- Sicher. Autark betriebene Reinräume mit separatem Klimatisierungs- und Filtersystem.
- Flexibel. Einzelteil- und Baugruppenkomissionierung sowie Montage.
- Qualifiziert. DIN EN ISO 14644 Klasse 7, GMP Standard – C.
- Wirtschaftlich. Kompaktes Layout, geringe Betriebskosten.
- Zertifiziert. Qualitätsmanagementsystem nach DIN EN ISO 13485:2016.
Montage- und Konfektionierungslösungen.
Unser Antrieb für optimierte Produktionsabläufe: Innovative, hoch dynamische Verfahrens- und Montagetechnik gehören seit jeher zum Standard. Aus gutem Grund, denn optimierte Produktionsprozesse helfen effektiv Kosten einzusparen – ganz gleich ob mittels vollautomatischer Montage- und Konfektionierungslösungen oder in den Produktionsablauf integrierte Verpackungslösungen.
Das beinhaltet die vollautomatische Entnahme der Bauteile aus dem Werkzeug sowie das Ablegen bzw. Stapeln der Artikel auf einem Förderband. Je nach Anwendungsfall gehören die vollautomatische Montage, eine Etikettierung sowie eine Konfektionierung zu den nachfolgenden Prozessen. Am Ende der Prozesskette erfolgt die Verpackung in eine mit dem Kunden abgestimmte Sekundärverpackung.
Die Vorteile auf einen Blick:
- Wirtschaftlich. Effektive Kosteneinsparung durch schlanke Prozesse.
- Sicher. Eigenverantwortliche Steuerung und Überwachung der unterschiedlichen Prozessschritte.
- Anspruchsvoll. Reduzierte Bauteilkontamination durch vollautomatische Prozesse.
- Prozesssicher. Konfektionierung in „Verkaufsverpackung“.
- Sauber. Baugruppenmontagen unter Reinraumbedingungen.
Fügetechnik – höhere Produktqualität, kürzere Taktzeiten.
Perfektion bis ins Detail: Dank modernster Montagetechniken sind wir in der Lage, individuelle Lösungen effizient für unsere Kunden zu realisieren. Vielseitige und praxiserprobte Verfahren wie das Heiß-Gas-Schweißen oder das Vibrationsschweißen gehören dabei zum Standard. Zeitgleich entwickeln wir den Bereich der Montagetechnik konsequent weiter, um auch in Zukunft zuverlässig und schnell zu liefern.
Bei komplexen Bauteil-Geometrien, die sich nicht in einem einzelnen Spritzguss-Werkzeug realisieren lassen, muss die Geometrie geteilt und anschließend wieder miteinander verbunden werden.
Bauteile mit anspruchsvoller Geometrie, die hohe Festigkeiten und eine hohe technische Sauberkeit erfordern, lassen sich besonders gut mittels Heißgasschweißen miteinander verbinden. Dabei werden beide Komponenten in der Fügezone mit Stickstoff erhitzt, der Kunststoff schmilzt und die Teile werden unter Druck zusammengefügt.
Im Gegensatz zum mechanischen Schweißen ist dieses thermische Schweißverfahren partikelfrei. Durch Einsatz von Schutzgas im Schweißnahtbereich wird eine Oxidation des Materials vermieden. Eine thermische Schädigung des Kunststoffs wird dadurch ausgeschlossen.
Ein weiteres Plus: Das Heiß-Gas-Schweiß-Verfahren kann bei einer Vielzahl von technischen Werkstoffen eingesetzt werden. Außerdem eignet sich das Verfahren auch für komplexe 3D-Geometrien.
Bei komplexen Bauteil-Geometrien, die sich nicht in einem einzelnen Spritzguss-Werkzeug realisieren lassen, muss die Geometrie geteilt und anschließend wieder miteinander verbunden werden.
Beim Ultraschallweißen werden zwei Kunststoffteile an der Fügezone miteinander verbunden. Durch mechanische Schwingungen entsteht eine Reibung an der Fügezone, die eine für das Schweißen notwendige Wärme erzeugt. Unter Druck werden die Kunststoffe werden unter Druck miteinander vereint.
Sind schnelle Prozesszeiten bei einer hohen Prozesssicherheit gefragt, ist das Ultraschallschweißen besonders vorteilhaft. Auch, weil keine Zusatzstoffe oder Lösungsmittel verwendet werden müssen.
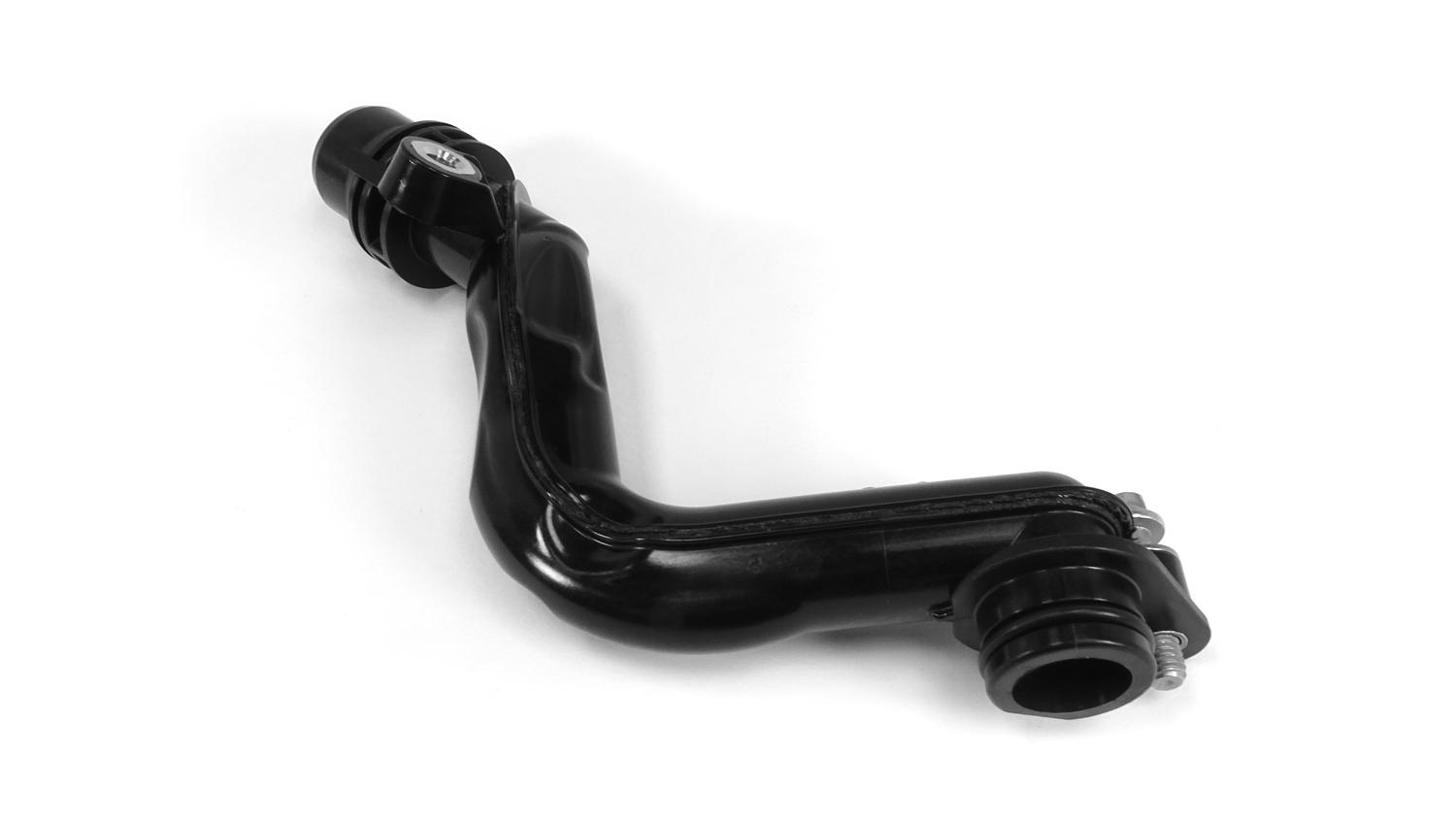

Bei komplexen Bauteil-Geometrien, die sich nicht in einem einzelnen Spritzguss-Werkzeug realisieren lassen, muss die Geometrie geteilt und anschließend wieder miteinander verbunden werden.
Das Laserschweißen eignet sich besonders für 2D Geometrien in Verbindung mit dem Quasi-Simultan-Schweißen oder bei Rundkörpern unter Einbezug des Radialschweißens. Beim Laserschweißen ist es notwendig, dass eine Komponente aus lasertransparentem und eine Komponente aus laserabsorbierendem Material besteht.
Der Laser dringt durch das transparente Material und bewirkt am anliegenden, absorbierenden Material das Aufschmelzen des Kunststoffes. Die Wärme, die dabei entsteht, wird an den oberen Schweißpartner weitergegeben, sodass beide Kunststoffe miteinander verschmelzen.
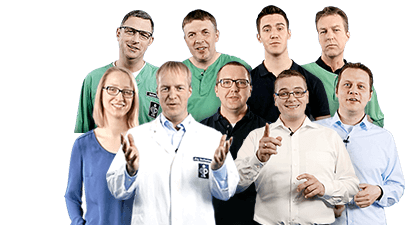
Wir machen den Unterschied.
Es sind nicht unsere Hallen, Maschinen oder Werkzeuge, die uns über die Jahrzehnte erfolgreich gemacht haben. Es sind unsere Mitarbeiter, die mit ihrem Wissen, ihrem leidenschaftlichen Einsatz und ihrem Streben nach Perfektion den Unterschied machen. Erleben Sie spannende und unterhaltsame Einblicke in ihre tägliche Arbeit.
Diese Themen könnten Sie auch interessieren:
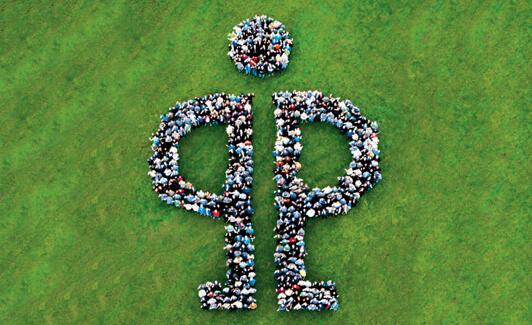
Wir machen den Unterschied
Lernen Sie uns kennen.
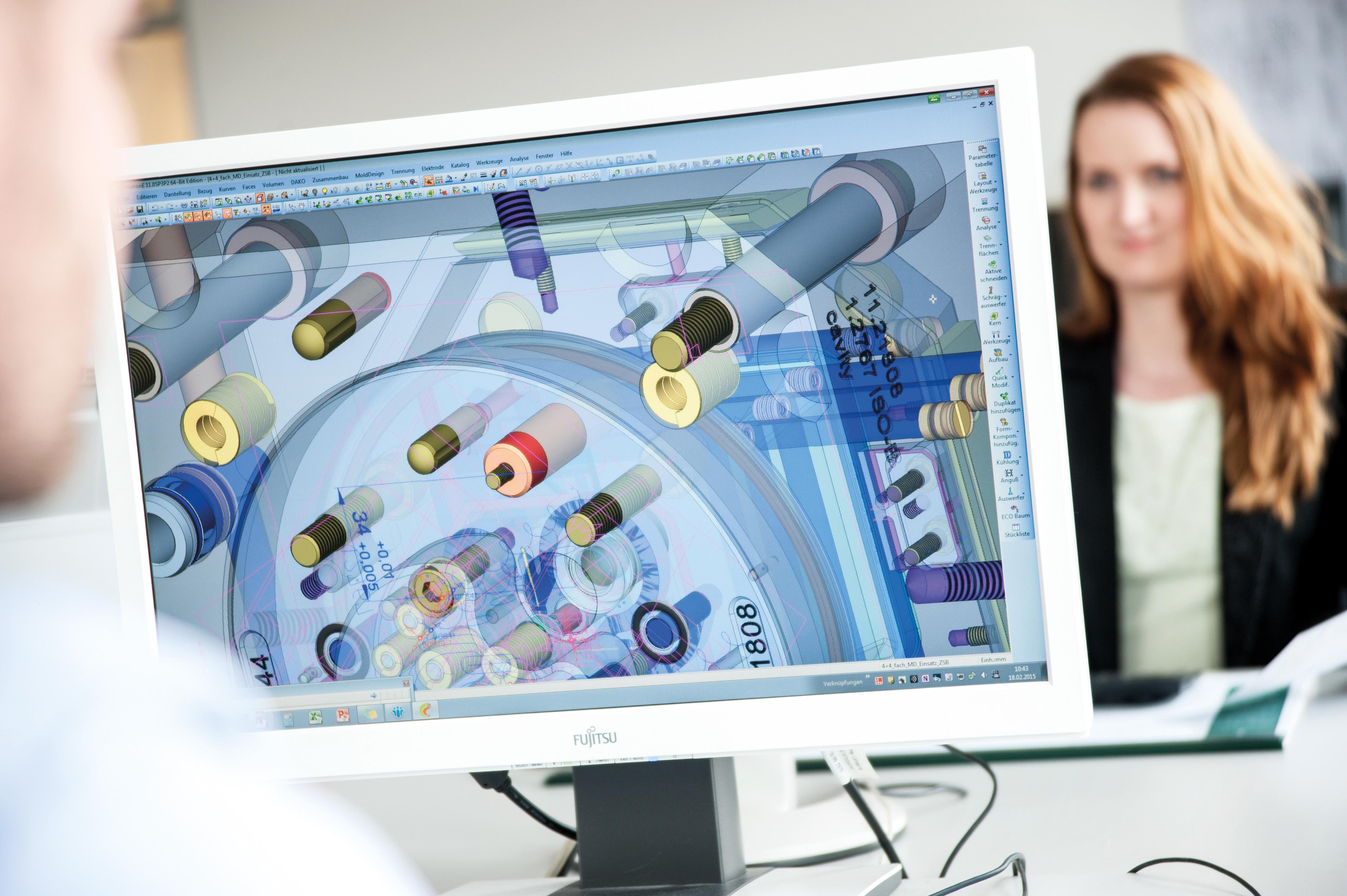
Entwicklung
Von der Entwicklung bis zur Serie.
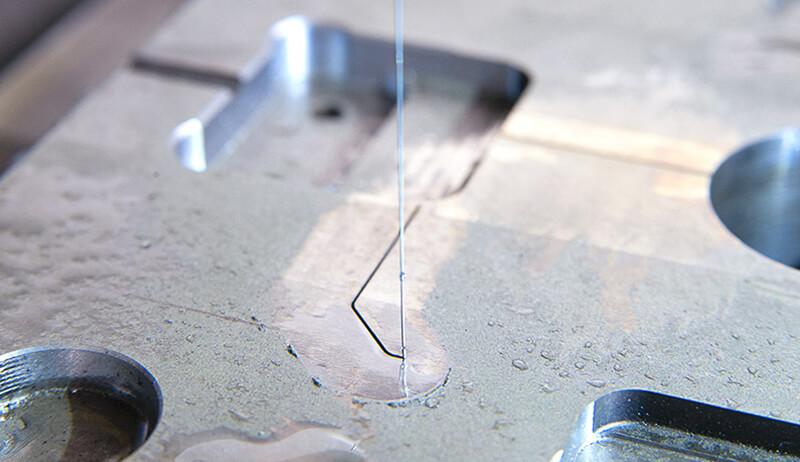
Eigener Werkzeugbau
Präzision als Basis.
Sie haben Fragen? Das FAMAC® Team beantwortet sie gerne.

Vor Ort
Unsere Vertriebsmitarbeiter kommen einfach zu Ihnen. Jetzt Termin vereinbaren.

+49 4442 982-3900
Montag bis Donnerstag: 8:00 –17:00 Uhr
Freitag: 8:00 – 15:30 Uhr

Per E-Mail
Rund um die Uhr. Wir melden uns so schnell wie möglich bei Ihnen zurück.